Sugarcane residue can also be used to make organic fertilizer.
Date:2024/08/10
In the exploration of sustainable agriculture and resource recycling, bagasse, which was once regarded as a waste material, is gradually showing its great potential as a raw material for organic fertilizer. Through the careful treatment of organic fertilizer production line, bagas can not only realize waste utilization, but also be converted into nutrient rich organic fertilizer, injecting new vitality into farmland.
The production and processing process of organic fertilizer revolves around the three core links of ripening, dehydration and granulation, and the addition of Sugarcaneadds new vitality to this process. On the Organic fertilizer production line, all kinds of advanced equipment work together to complete this green transformation.
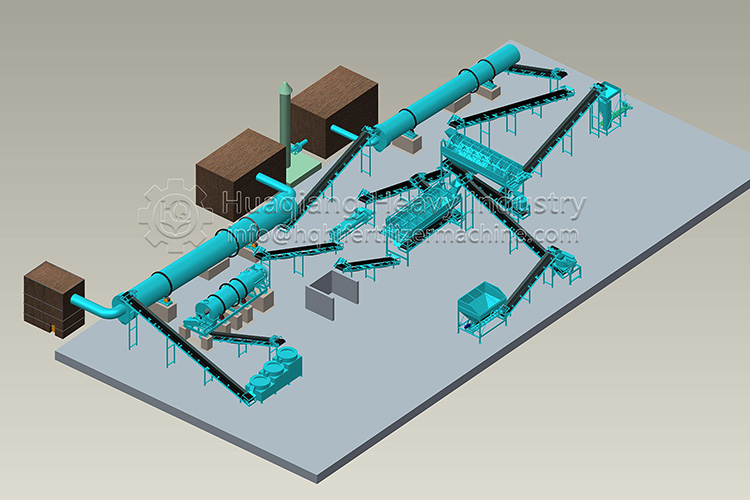
Ripening stage: bagars are first mixed with appropriate amount of water, and regularly turned and aerated by organic fertilizer fermentation equipment -- Windrow Compost Turning Machine. This process promoted the activity of microorganisms, accelerated the decomposition and decay of organic matter in bagasse, and laid a good foundation for subsequent treatment.
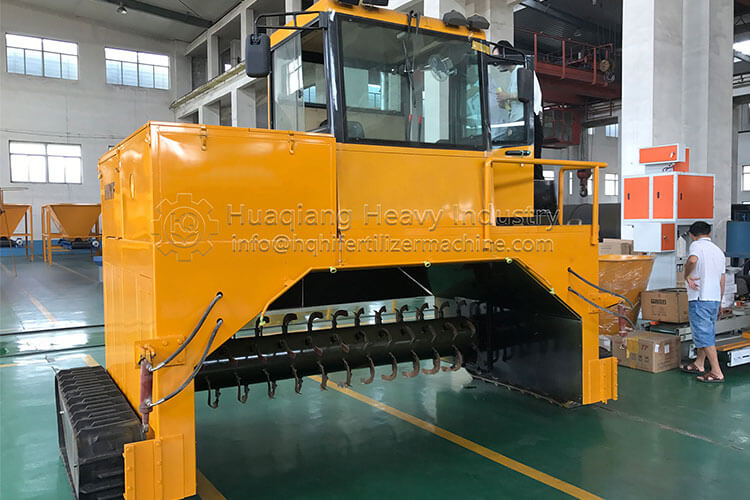
Crushing and stirring: The decomposed Sugarcaneraw materials should be treated by a crusher. According to the humidity and characteristics of the raw materials, appropriate vertical or horizontal crusher should be selected for crushing. Subsequently, the Sugarcanewas thoroughly mixed with other organic materials using a blender (vertical or horizontal, uniaxial or biaxial) to ensure an even distribution of nutrients.
Screening and transportation: after crushing and stirring materials, through the roller screen or vibration grading screen for screening, remove impurities, improve product quality. Subsequently, the large Angle belt conveyor or screw conveyor will be screened after the material to the next process.
Pelleting and molding: In the pelleting process, Fertilizer Granules Compaction Machine with its unique double-roll extrusion technology, the Sugarcaneis mixed with other organic materials and extrudated into pellets. This step not only enhances the appearance and market value of the product, but also facilitates subsequent storage, transportation, and use. Of course, according to the market demand, some manufacturers will also choose to make the material directly into powder or extrusion into columns.
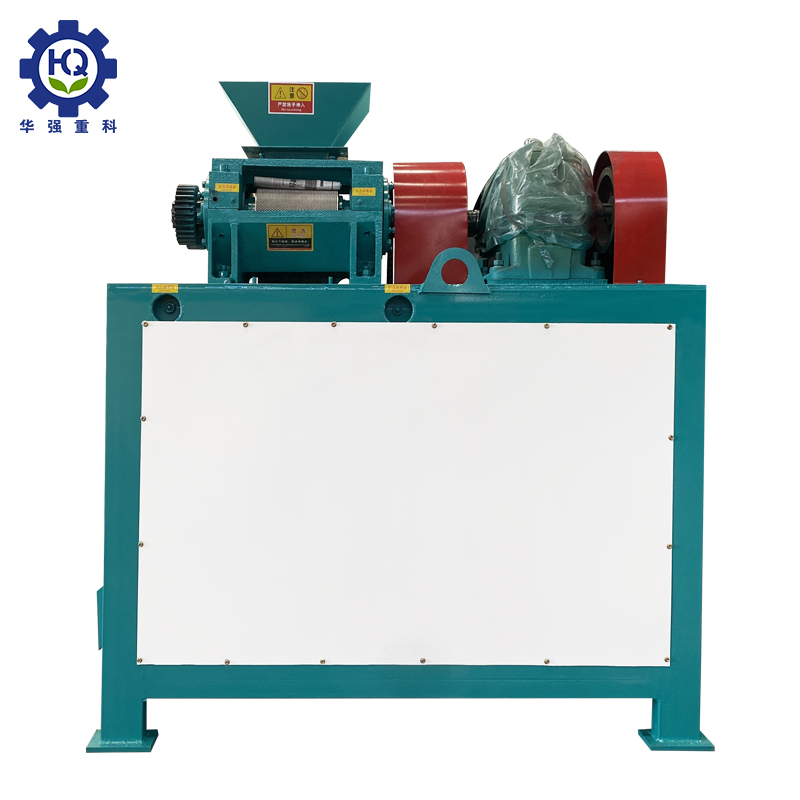
Drying and cooling: The organic fertilizer after granulation needs to be dried by a roller dryer to reduce moisture content and improve stability. A drum cooling machine is then responsible for cooling the dried particles to the appropriate temperature to avoid nutrient damage from overheating.
Packaging and sale: Finally, with the cooperation of automatic batching machine, conveyor and quantitative packaging scale and other equipment, the dried and cooled organic fertilizer is accurately measured and packaged into bags, ready to be sold to farmers or agricultural enterprises.
The green value of bagasse
The application of Sugarcaneas raw material of organic fertilizer not only realizes the resource utilization of agricultural waste, reduces environmental pollution, but also promotes the improvement of soil structure and the increase of crop yield. It is rich in cellulose, hemicellulose and mineral elements, which can release nutrients slowly in the soil and provide lasting and comprehensive nutritional support for plants.
The application of Sugarcanein organic fertilizer production is a vivid practice of agricultural circular economy. Through advanced organic fertilizer production lines and supporting equipment, we can convert this waste into valuable agricultural resources and contribute to the realization of sustainable agricultural development.
The production and processing process of organic fertilizer revolves around the three core links of ripening, dehydration and granulation, and the addition of Sugarcaneadds new vitality to this process. On the Organic fertilizer production line, all kinds of advanced equipment work together to complete this green transformation.
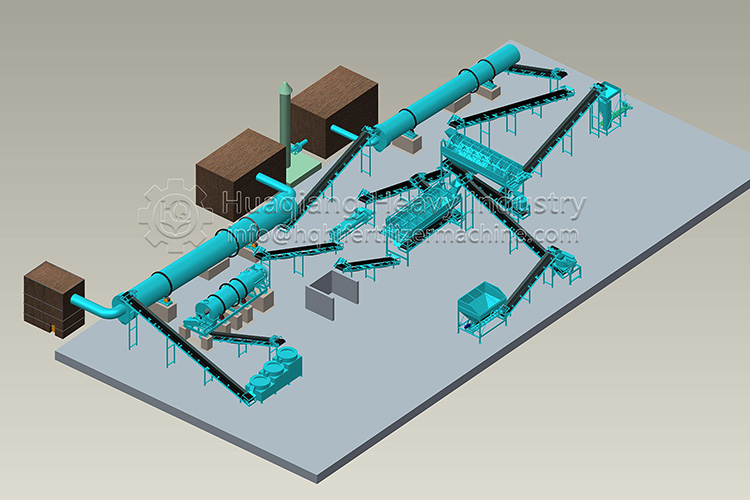
Ripening stage: bagars are first mixed with appropriate amount of water, and regularly turned and aerated by organic fertilizer fermentation equipment -- Windrow Compost Turning Machine. This process promoted the activity of microorganisms, accelerated the decomposition and decay of organic matter in bagasse, and laid a good foundation for subsequent treatment.
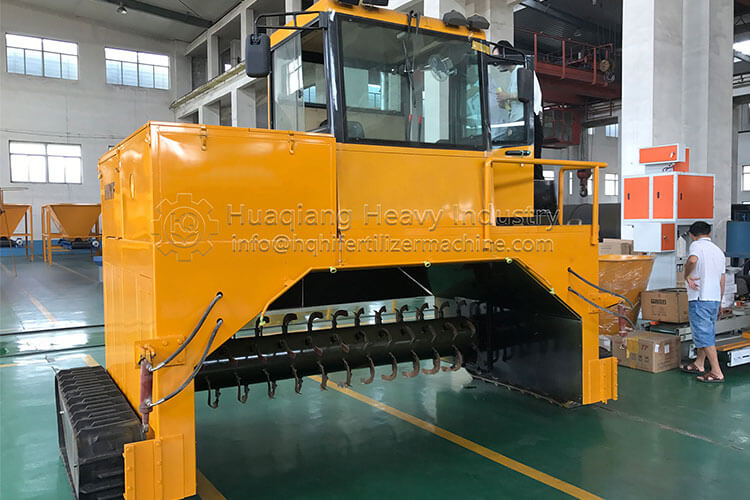
Crushing and stirring: The decomposed Sugarcaneraw materials should be treated by a crusher. According to the humidity and characteristics of the raw materials, appropriate vertical or horizontal crusher should be selected for crushing. Subsequently, the Sugarcanewas thoroughly mixed with other organic materials using a blender (vertical or horizontal, uniaxial or biaxial) to ensure an even distribution of nutrients.
Screening and transportation: after crushing and stirring materials, through the roller screen or vibration grading screen for screening, remove impurities, improve product quality. Subsequently, the large Angle belt conveyor or screw conveyor will be screened after the material to the next process.
Pelleting and molding: In the pelleting process, Fertilizer Granules Compaction Machine with its unique double-roll extrusion technology, the Sugarcaneis mixed with other organic materials and extrudated into pellets. This step not only enhances the appearance and market value of the product, but also facilitates subsequent storage, transportation, and use. Of course, according to the market demand, some manufacturers will also choose to make the material directly into powder or extrusion into columns.
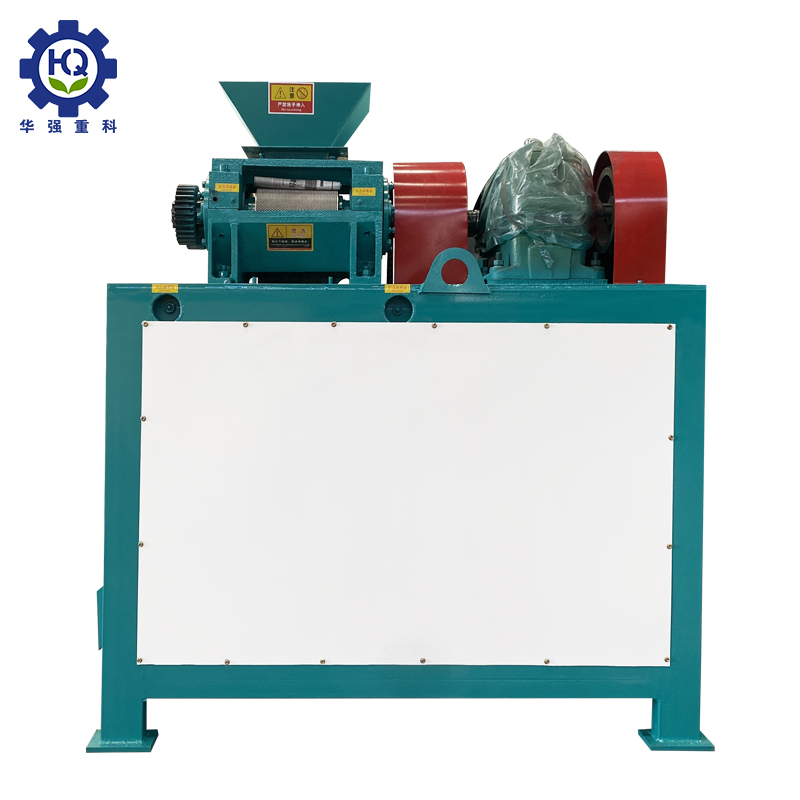
Drying and cooling: The organic fertilizer after granulation needs to be dried by a roller dryer to reduce moisture content and improve stability. A drum cooling machine is then responsible for cooling the dried particles to the appropriate temperature to avoid nutrient damage from overheating.
Packaging and sale: Finally, with the cooperation of automatic batching machine, conveyor and quantitative packaging scale and other equipment, the dried and cooled organic fertilizer is accurately measured and packaged into bags, ready to be sold to farmers or agricultural enterprises.
The green value of bagasse
The application of Sugarcaneas raw material of organic fertilizer not only realizes the resource utilization of agricultural waste, reduces environmental pollution, but also promotes the improvement of soil structure and the increase of crop yield. It is rich in cellulose, hemicellulose and mineral elements, which can release nutrients slowly in the soil and provide lasting and comprehensive nutritional support for plants.
The application of Sugarcanein organic fertilizer production is a vivid practice of agricultural circular economy. Through advanced organic fertilizer production lines and supporting equipment, we can convert this waste into valuable agricultural resources and contribute to the realization of sustainable agricultural development.