Rotary drum granulator technology and application advanced
Date:2024/07/09
In the field of modern fertilizer production, drum granulator is an efficient and multi-functional equipment, and the continuous advancement of its process and application is an important force to promote the development of the fertilizer industry. This chapter will explore in depth the latest technological progress of the drum granulator, while connecting a number of key equipment and systems to build an efficient and environmentally friendly fertilizer production line.
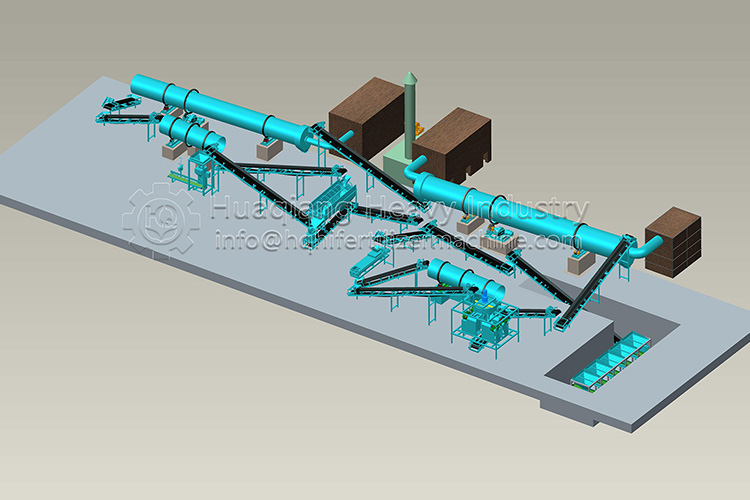
1.Rotary drum granulator technology innovation
As the core equipment, the Rotary Drum Granulator realizes the efficient granulation of various raw materials through its unique rotating drum structure and internal scraper system. With the advancement of technology, the newly designed drum granulator is integrated with an intelligent control system, which can automatically adjust the speed, temperature and humidity to ensure stable and uniform particle quality. In addition, combined with the use of the round polishing machine, the roundness and surface smoothness of the particles are further improved, meeting the market demand for high-quality fertilizers.
2. the synergy of front-end preprocessing equipment
Pretreatment of raw materials is very important before Rotary Drum Granulation. Equipment such as Chain Crusher, Half-Wet Material Crusher, Cage Crusher and Straw Crusher can efficiently break bulk raw materials to the appropriate particle size, laying a good foundation for the subsequent granulation process. In particular, the Single Axis Urea Crusher has a unique crushing effect for easily caked materials such as urea, ensuring the uniformity and fluidity of raw materials.
3.Optimization of mixing and conveying system
Mixing equipment, such as Horizontal Mixer, Vertical Disc Mixer and Double Axis Mixer, ensure the full mixing of raw materials before granulation, improve the uniformity and consistency of products. The BB Fertilizer Blender is specially designed for the production of compound fertilizers, which can quickly and evenly mix a variety of raw materials. The Belt Conveyor, Mobile Belt Conveyor, Bucket Elevator, Large Angle Belt Conveyor and Screw Conveyor and other conveying equipment, to build an efficient and flexible material transmission network, to ensure the continuity and stability of the production line.
4.Upgrading of screening and post-processing equipment
Drum Screener Machine and Vibration Screener Machine as screening equipment, effectively remove the fine powder and unqualified particles produced in the granulation process, improve product quality. Drum Fertilizer Dryer and Drum Fertilizer Cooler are responsible for drying and cooling the particles respectively, ensuring that the product reaches the ideal moisture content and temperature for easy storage and transportation. In addition, the application of the Coating Machine provides anti-caking, slow release and other characteristics for fertilizer particles, which further enhances the market competitiveness of the product.
5. environmental protection and auxiliary equipment improvement
While pursuing efficient production, environmental protection and energy saving have also become important considerations for fertilizer production lines. Stacking equipment such as Simple Compost Turning Machine, Hydraulic Compost Turning Machine and Double Screws Compost Turning Machine can optimize the composting process of organic waste and reduce environmental pollution. Auxiliary equipment such as Loader Feeding Hopper and Uniform Feeder improve the automation level of the production line. The Dewatering Machine, Gas/Oil Hot Air Stove, Steam Boiler, Cyclone Dust Collector and Melting Pot and other equipment have played an important role in energy saving and emission reduction and resource recycling.
6.Intelligent automatic batching and packaging system
The application of the Multiple Silos Single Weigh Static Automatic Batching System and the Single Silo Single Weigh Dynamic Automatic Batching System realize the precise control of the ratio of raw materials and improves the production efficiency and product quality. Powder/Granular Fertilizer Packing Machine and Tons Bag Fertilizer Packing Machine meet the packaging needs of different specifications of products, improve the overall automation level of the production line.
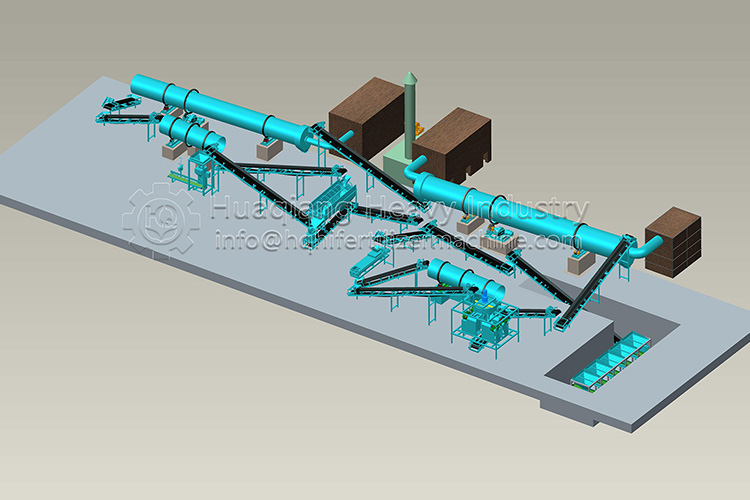
1.Rotary drum granulator technology innovation
As the core equipment, the Rotary Drum Granulator realizes the efficient granulation of various raw materials through its unique rotating drum structure and internal scraper system. With the advancement of technology, the newly designed drum granulator is integrated with an intelligent control system, which can automatically adjust the speed, temperature and humidity to ensure stable and uniform particle quality. In addition, combined with the use of the round polishing machine, the roundness and surface smoothness of the particles are further improved, meeting the market demand for high-quality fertilizers.
2. the synergy of front-end preprocessing equipment
Pretreatment of raw materials is very important before Rotary Drum Granulation. Equipment such as Chain Crusher, Half-Wet Material Crusher, Cage Crusher and Straw Crusher can efficiently break bulk raw materials to the appropriate particle size, laying a good foundation for the subsequent granulation process. In particular, the Single Axis Urea Crusher has a unique crushing effect for easily caked materials such as urea, ensuring the uniformity and fluidity of raw materials.
3.Optimization of mixing and conveying system
Mixing equipment, such as Horizontal Mixer, Vertical Disc Mixer and Double Axis Mixer, ensure the full mixing of raw materials before granulation, improve the uniformity and consistency of products. The BB Fertilizer Blender is specially designed for the production of compound fertilizers, which can quickly and evenly mix a variety of raw materials. The Belt Conveyor, Mobile Belt Conveyor, Bucket Elevator, Large Angle Belt Conveyor and Screw Conveyor and other conveying equipment, to build an efficient and flexible material transmission network, to ensure the continuity and stability of the production line.
4.Upgrading of screening and post-processing equipment
Drum Screener Machine and Vibration Screener Machine as screening equipment, effectively remove the fine powder and unqualified particles produced in the granulation process, improve product quality. Drum Fertilizer Dryer and Drum Fertilizer Cooler are responsible for drying and cooling the particles respectively, ensuring that the product reaches the ideal moisture content and temperature for easy storage and transportation. In addition, the application of the Coating Machine provides anti-caking, slow release and other characteristics for fertilizer particles, which further enhances the market competitiveness of the product.
5. environmental protection and auxiliary equipment improvement
While pursuing efficient production, environmental protection and energy saving have also become important considerations for fertilizer production lines. Stacking equipment such as Simple Compost Turning Machine, Hydraulic Compost Turning Machine and Double Screws Compost Turning Machine can optimize the composting process of organic waste and reduce environmental pollution. Auxiliary equipment such as Loader Feeding Hopper and Uniform Feeder improve the automation level of the production line. The Dewatering Machine, Gas/Oil Hot Air Stove, Steam Boiler, Cyclone Dust Collector and Melting Pot and other equipment have played an important role in energy saving and emission reduction and resource recycling.
6.Intelligent automatic batching and packaging system
The application of the Multiple Silos Single Weigh Static Automatic Batching System and the Single Silo Single Weigh Dynamic Automatic Batching System realize the precise control of the ratio of raw materials and improves the production efficiency and product quality. Powder/Granular Fertilizer Packing Machine and Tons Bag Fertilizer Packing Machine meet the packaging needs of different specifications of products, improve the overall automation level of the production line.