Key elements of organic fertilizer granulator selection
Date:2024/07/10
In the field of organic fertilizer production, choosing the right granulator is a key step to ensure product quality, improve production efficiency and reduce operating costs. The selection of organic fertilizer granulator is a process that considers many factors comprehensively. Through in-depth analysis of material characteristics, production capacity, granulation effect, energy consumption and environmental protection, maintenance and after-sales service and other factors. Through scientific and reasonable selection, the production efficiency, product quality and market competitiveness of organic fertilizer production enterprises can be significantly improved.
Material characteristics and equipment selection
Material characteristics are the basis of selection. Different types of organic waste (such as livestock and poultry manure, crop straw, bacterial residue, etc.) have differences in water content, viscosity, particle size, etc., which directly affect the applicability of pelletizer and pelletization effect. Therefore, before selecting a granulator, it is necessary to conduct a comprehensive analysis of the raw materials to ensure that the selected equipment can effectively handle the target material. For example, for materials with high humidity, you can choose a New Type Two-In-One Organic Fertilizer Granulator or a Rotary Drum Granulator, which can effectively handle sticky materials and reduce sticky wall phenomena. For raw materials with larger particle size, pre-treatment can be carried out first, and equipment such as Chain Crusher and Straw Crusher can be refined to improve the pelletizing effect.
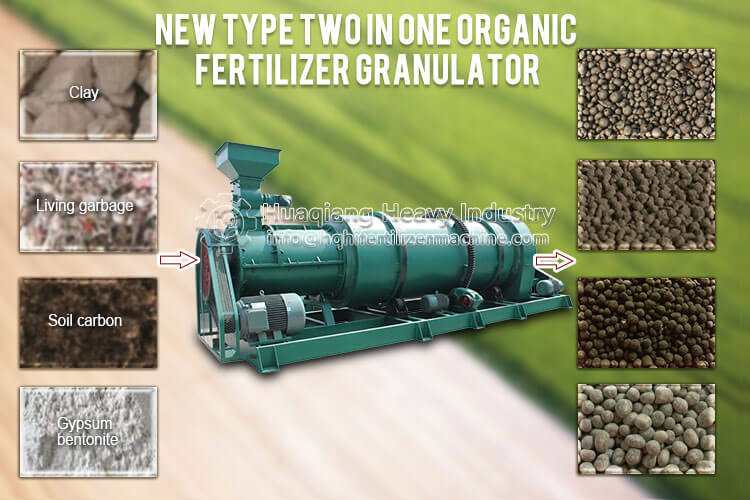
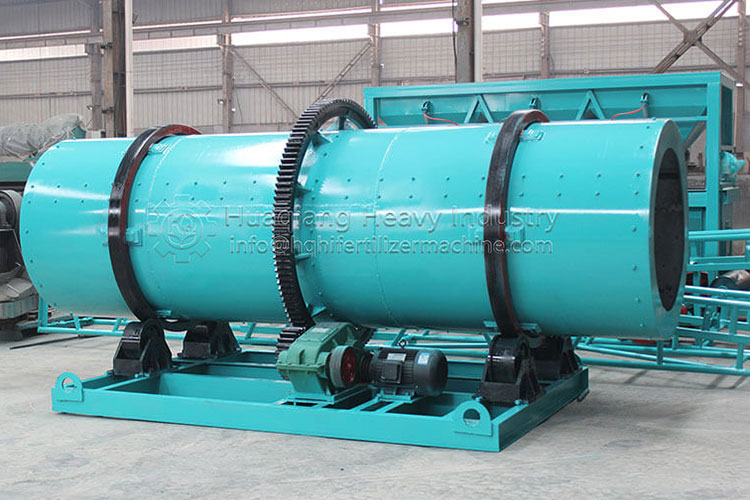
Production capacity and equipment specifications
After determining the production capacity according to the production scale and market demand, the granulator of the corresponding specifications should be selected. For large-scale production, Hydraulic Roller Granulator、Double Roller Press Granulator、 Disc Granulaor (Pan Granulator) or Flat Die Granulator are preferred due to their efficient and stable performance. These devices are able to meet high yield requirements while maintaining particle quality.
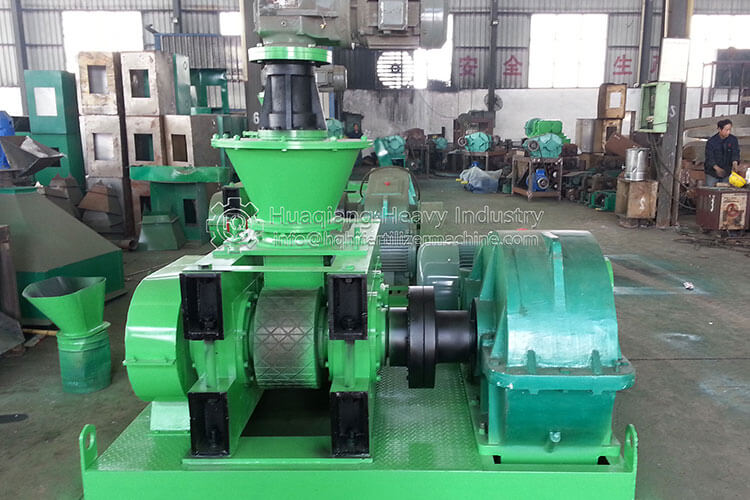
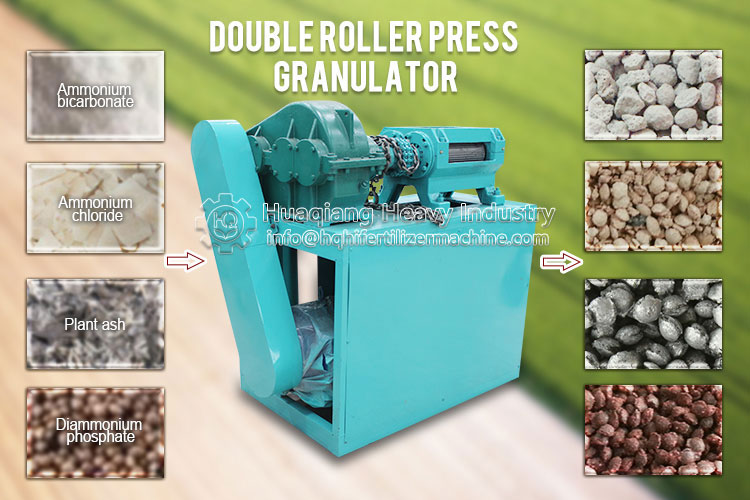
Granulation effect and equipment optimization
In pursuit of good granulation effect, it is necessary to pay attention to the granulation principle and mold design of the equipment. For example, the New Type Organic Fertilizer Granulator can produce organic fertilizer particles with high uniformity, good strength and good roundness by optimizing the mold structure. In addition, the Ball Shaping Machine can be used for secondary shaping of the initially formed particles to further improve the appearance quality of the product.
Energy consumption, environmental protection and equipment selection
Choosing a granulator with low energy consumption, high efficiency and environmental protection standards helps to reduce production costs, reduce environmental burden and meet the requirements of modern agricultural production. Hydraulic Roller Granulators are favored for their low energy consumption characteristics, while all equipment should be operated with noise control and dust collection in mind, such as equipped with an effective dust removal system.
Maintenance and after-sales service
Good maintenance can extend the service life of the equipment and reduce the failure rate; The perfect after-sales service can provide timely solutions and technical support when the equipment has problems. Therefore, in the selection, we should understand the supplier's service system, parts supply and user reputation and other information. For example, regular inspection and maintenance of equipment, as well as the use of auxiliary equipment such as Belt Conveyors and Bucket Elevators to optimize the layout of the production line, reduce manual intervention, and improve overall operational efficiency.
Material characteristics and equipment selection
Material characteristics are the basis of selection. Different types of organic waste (such as livestock and poultry manure, crop straw, bacterial residue, etc.) have differences in water content, viscosity, particle size, etc., which directly affect the applicability of pelletizer and pelletization effect. Therefore, before selecting a granulator, it is necessary to conduct a comprehensive analysis of the raw materials to ensure that the selected equipment can effectively handle the target material. For example, for materials with high humidity, you can choose a New Type Two-In-One Organic Fertilizer Granulator or a Rotary Drum Granulator, which can effectively handle sticky materials and reduce sticky wall phenomena. For raw materials with larger particle size, pre-treatment can be carried out first, and equipment such as Chain Crusher and Straw Crusher can be refined to improve the pelletizing effect.
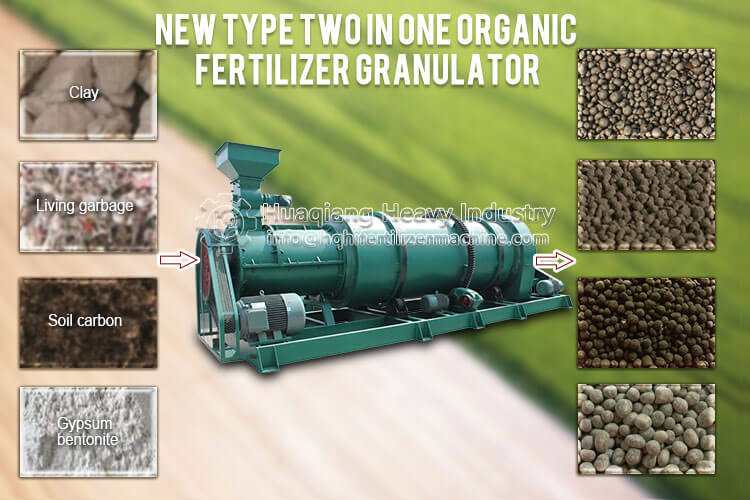
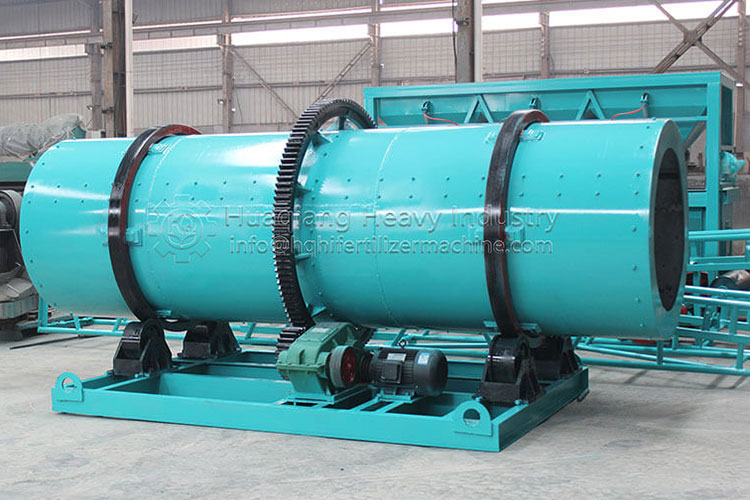
Production capacity and equipment specifications
After determining the production capacity according to the production scale and market demand, the granulator of the corresponding specifications should be selected. For large-scale production, Hydraulic Roller Granulator、Double Roller Press Granulator、 Disc Granulaor (Pan Granulator) or Flat Die Granulator are preferred due to their efficient and stable performance. These devices are able to meet high yield requirements while maintaining particle quality.
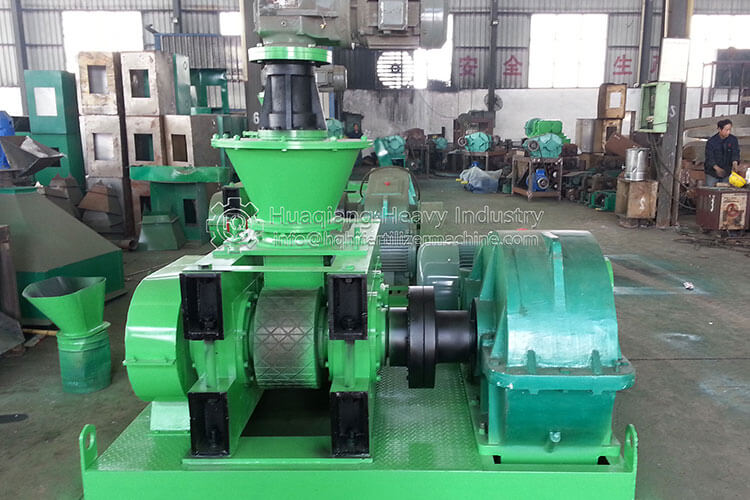
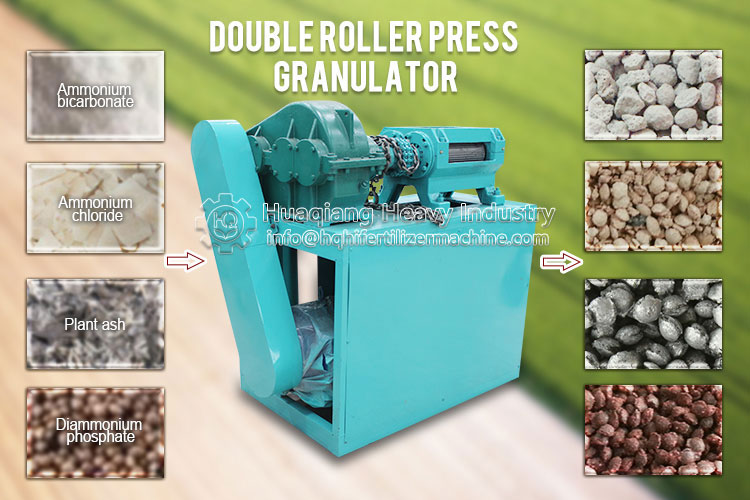
Granulation effect and equipment optimization
In pursuit of good granulation effect, it is necessary to pay attention to the granulation principle and mold design of the equipment. For example, the New Type Organic Fertilizer Granulator can produce organic fertilizer particles with high uniformity, good strength and good roundness by optimizing the mold structure. In addition, the Ball Shaping Machine can be used for secondary shaping of the initially formed particles to further improve the appearance quality of the product.
Energy consumption, environmental protection and equipment selection
Choosing a granulator with low energy consumption, high efficiency and environmental protection standards helps to reduce production costs, reduce environmental burden and meet the requirements of modern agricultural production. Hydraulic Roller Granulators are favored for their low energy consumption characteristics, while all equipment should be operated with noise control and dust collection in mind, such as equipped with an effective dust removal system.
Maintenance and after-sales service
Good maintenance can extend the service life of the equipment and reduce the failure rate; The perfect after-sales service can provide timely solutions and technical support when the equipment has problems. Therefore, in the selection, we should understand the supplier's service system, parts supply and user reputation and other information. For example, regular inspection and maintenance of equipment, as well as the use of auxiliary equipment such as Belt Conveyors and Bucket Elevators to optimize the layout of the production line, reduce manual intervention, and improve overall operational efficiency.