Diversified selection strategy of organic fertilizer granulator
Date:2024/07/11
In the field of organic fertilizer production, with the improvement of agricultural modernization and environmental awareness, the diversified selection strategy of organic fertilizer granulator is particularly important.The diversified selection strategy of organic fertilizer pelletizer needs to consider many factors such as production scale, raw material characteristics, cost effectiveness and follow-up treatment needs. Through scientific selection and reasonable configuration, it can not only improve production efficiency, but also ensure product quality, and promote the development of organic fertilizer industry to a more efficient and environmentally friendly direction.
First, the granulator selection and raw material characteristics match
For different raw material characteristics, such as water content, viscosity and particle formation difficulty, it is important to choose the right granulator. For example, for organic waste with moderate water content and easy molding, such as livestock and poultry manure, Flat die pelleting machine and Disc Granulator (Pan Granulator) can efficiently extrude materials into pellets, which is simple in structure and convenient in operation, suitable for small and medium-sized organic fertilizer plants. For high-humidity, high-viscosity materials, such as kitchen waste, Rotary Drum Granulator can rely on its powerful mixing and molding capabilities to achieve continuous production and improve production efficiency.
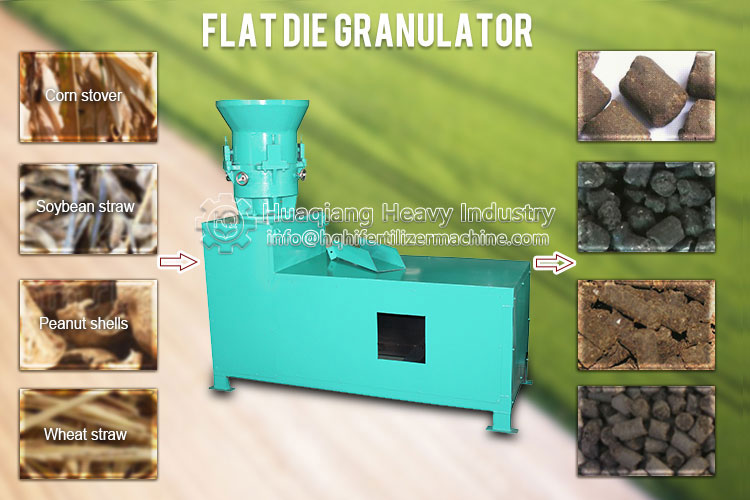
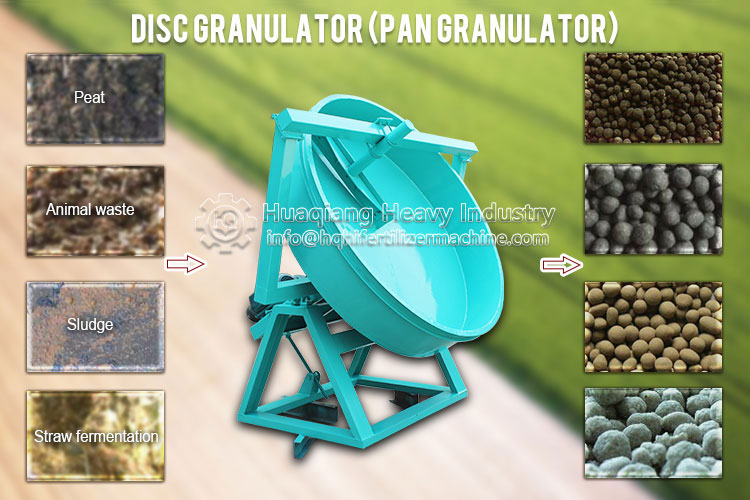
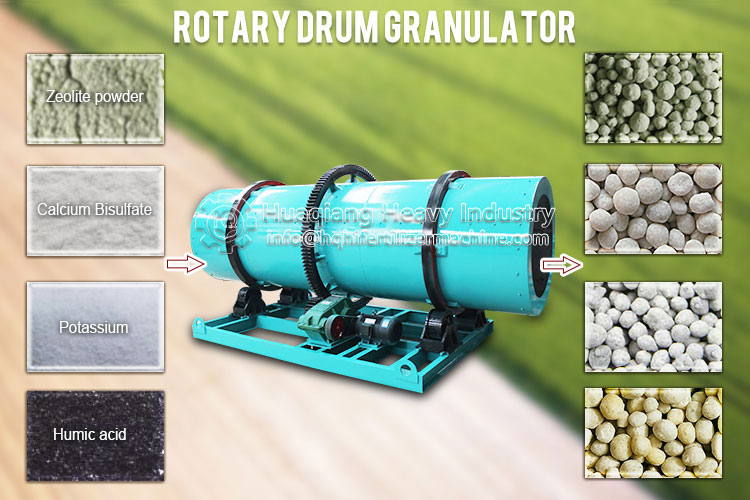
Second, optimize the production efficiency of pre-treatment equipment
Before granulation, the pretreatment of raw materials can not be ignored. The use of chain crusher, half-wet material crusher, straw crusher and other efficient crushing equipment can effectively reduce the size of the material, improve the mixing uniformity, and lay a good foundation for the subsequent granulation process. In particular, the single-axis urea crusher, in the mixing of fertilizer and organic materials, can ensure that the urea particles are fine and uniform, and promote the rapid release of nutrients.
Third, mixing to ensure uniform quality
Mixing is the key link to ensure the uniformity of organic fertilizer quality. Horizontal mixer, vertical disc mixer, double axis mixer and BB fertilizer mixer have their own characteristics, which can achieve full mixing of materials according to different formulations and process requirements. Among them, the two-axis mixer, with its powerful mixing capacity and wide adaptability, is especially suitable for large-scale production lines to ensure that each grain of fertilizer can achieve the best nutrient ratio.
Fourth, Intelligent upgrade of conveying and screening system
In the production line, belt conveyor, mobile belt conveyor, bucket elevator, large Angle belt conveyor and screw conveyor and other conveying equipment, to build an efficient and smooth material transmission network. The Drum screener machine and vibration screener are responsible for accurate screening, removing impurities and ensuring the quality of the finished product. The intelligent upgrading of these equipment, such as automatic speed adjustment, remote monitoring, etc., further improves the automation level of the production line and production efficiency.
Fifth, post-processing to strengthen product performance
The organic fertilizer after granulation needs to be dried by a Drum Fertilizer Dryer to remove excess water and prevent mildew. Subsequently, the Drum Fertilizer Cooler quickly reduces the temperature of the material and maintains particle stability. For specific needs, such as slow-release fertilizer production, the application of the Coating Machine can wrap a protective film on the outer layer of fertilizer particles, control the release rate of nutrients, and extend the fertilizer effect period.
First, the granulator selection and raw material characteristics match
For different raw material characteristics, such as water content, viscosity and particle formation difficulty, it is important to choose the right granulator. For example, for organic waste with moderate water content and easy molding, such as livestock and poultry manure, Flat die pelleting machine and Disc Granulator (Pan Granulator) can efficiently extrude materials into pellets, which is simple in structure and convenient in operation, suitable for small and medium-sized organic fertilizer plants. For high-humidity, high-viscosity materials, such as kitchen waste, Rotary Drum Granulator can rely on its powerful mixing and molding capabilities to achieve continuous production and improve production efficiency.
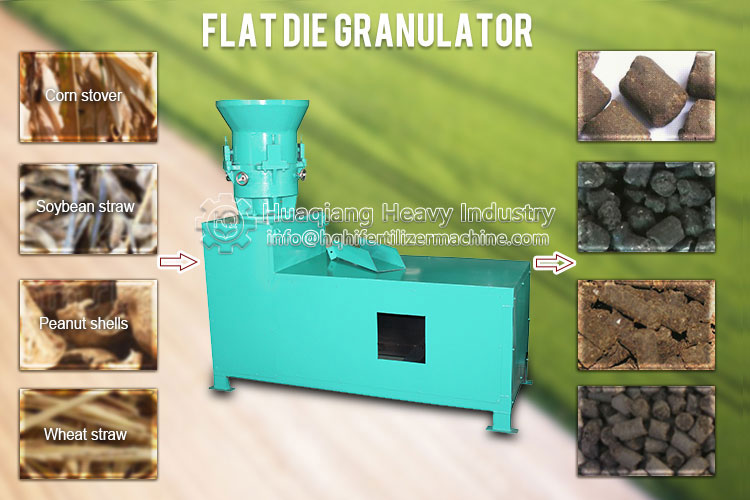
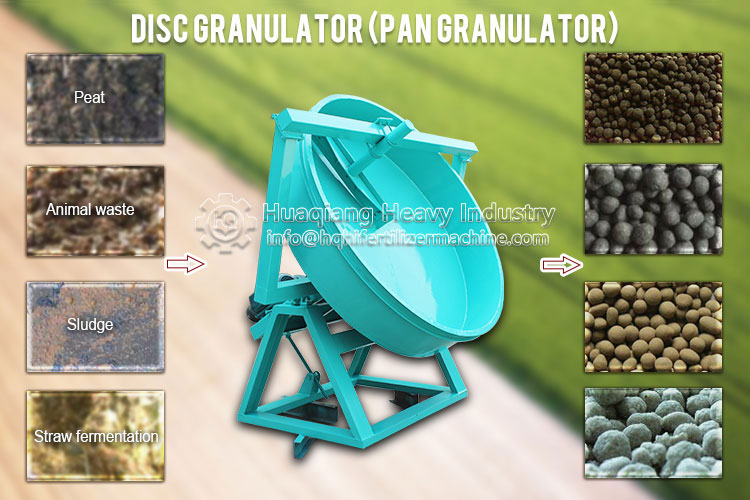
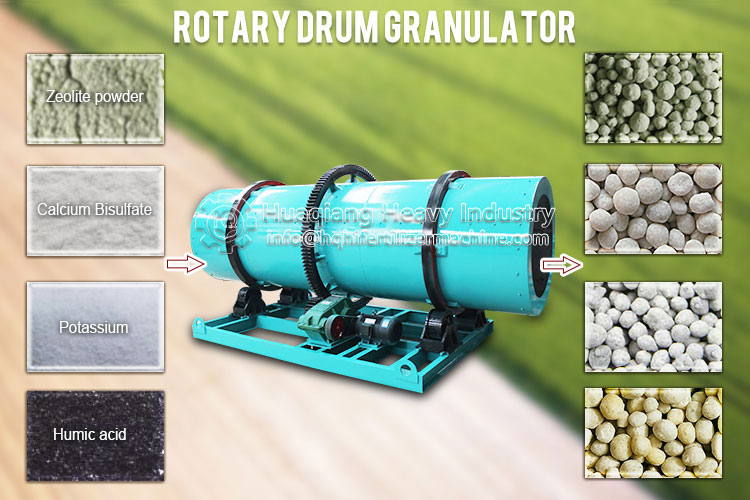
Second, optimize the production efficiency of pre-treatment equipment
Before granulation, the pretreatment of raw materials can not be ignored. The use of chain crusher, half-wet material crusher, straw crusher and other efficient crushing equipment can effectively reduce the size of the material, improve the mixing uniformity, and lay a good foundation for the subsequent granulation process. In particular, the single-axis urea crusher, in the mixing of fertilizer and organic materials, can ensure that the urea particles are fine and uniform, and promote the rapid release of nutrients.
Third, mixing to ensure uniform quality
Mixing is the key link to ensure the uniformity of organic fertilizer quality. Horizontal mixer, vertical disc mixer, double axis mixer and BB fertilizer mixer have their own characteristics, which can achieve full mixing of materials according to different formulations and process requirements. Among them, the two-axis mixer, with its powerful mixing capacity and wide adaptability, is especially suitable for large-scale production lines to ensure that each grain of fertilizer can achieve the best nutrient ratio.
Fourth, Intelligent upgrade of conveying and screening system
In the production line, belt conveyor, mobile belt conveyor, bucket elevator, large Angle belt conveyor and screw conveyor and other conveying equipment, to build an efficient and smooth material transmission network. The Drum screener machine and vibration screener are responsible for accurate screening, removing impurities and ensuring the quality of the finished product. The intelligent upgrading of these equipment, such as automatic speed adjustment, remote monitoring, etc., further improves the automation level of the production line and production efficiency.
Fifth, post-processing to strengthen product performance
The organic fertilizer after granulation needs to be dried by a Drum Fertilizer Dryer to remove excess water and prevent mildew. Subsequently, the Drum Fertilizer Cooler quickly reduces the temperature of the material and maintains particle stability. For specific needs, such as slow-release fertilizer production, the application of the Coating Machine can wrap a protective film on the outer layer of fertilizer particles, control the release rate of nutrients, and extend the fertilizer effect period.