Comparison and selection of performance of disc granulator and drum granulator
Date:2024/07/12
In the field of organic fertilizer production, Disc Granulator (Pan Granulator) and Rotary Drum Granulator as two mainstream granulation equipment, each has unique performance characteristics and scope of application.
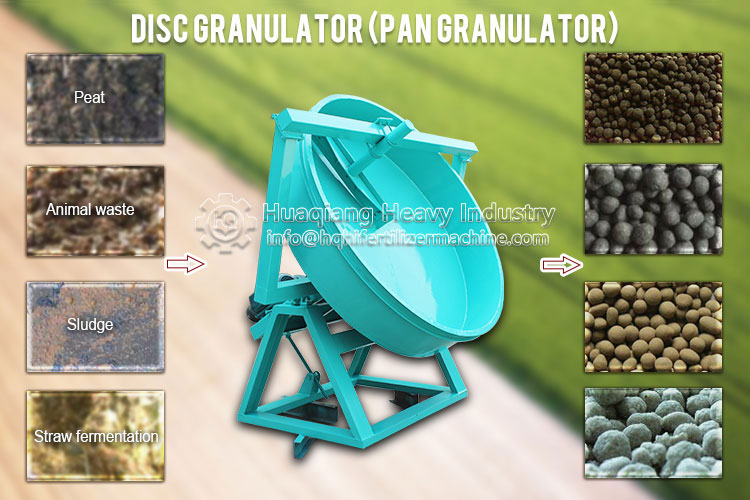
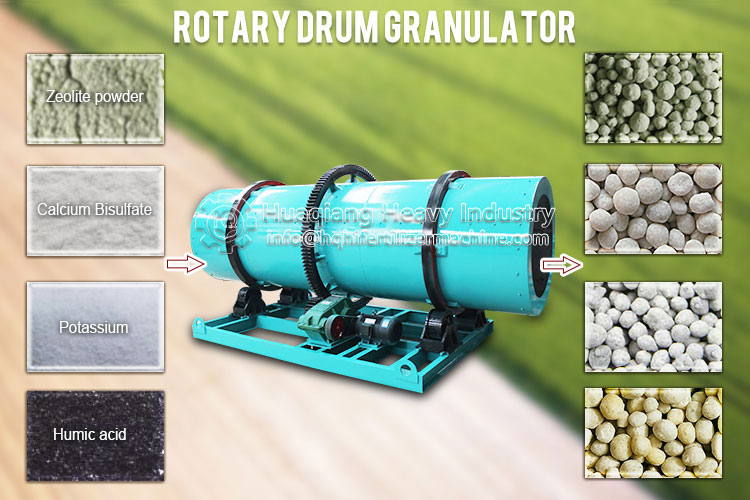
1.Comparison of processing capacity
Disc Granulator with its large working area and moderate speed, good at handling medium humidity, easy to form organic materials. Its continuous operation ability is strong, especially suitable for stable production on large-scale production lines. In contrast, the Rotary Drum Granulator, through its unique rotating structure and internal mixing device, can more effectively deal with high humidity and high viscosity materials to achieve efficient mixing and molding. When dealing with difficult materials, the Rotary Drum Granulator shows greater adaptability and processing capacity.
2. energy efficiency analysis
From the point of view of energy consumption, the Disc Granulator usually has a lower level of energy consumption due to its simple mechanical structure and low operating resistance. However, when handling high moisture materials, additional drying equipment (Drum Fertilizer Dryer) may be required, thus increasing the overall energy consumption. Through its optimized internal structure and efficient mixing mechanism, the Rotary Drum Granulator can reduce energy consumption to a certain extent, especially when dealing with high wet materials, its energy consumption efficiency is relatively higher. However, it is worth noting that the initial investment cost of the Rotary Drum Granulator may be relatively high.
3. Granulation effect evaluation
The granulation effect is one of the important indexes to measure the performance of granulation equipment. The Disc Granulator through its disc surface rolling and friction, so that the material gradually gathered into a ball, the granulation process is relatively mild, the particle shape is more regular, the surface is smooth. The Rotary Drum Granulator through its internal mixing and rolling action, so that the material in the rotation process by strong shear and extrusion, the formation of more compact, uniform particles. In the pursuit of high particle strength and wear resistance, the Rotary Drum Granulator is more advantageous.
4. Maintenance cost consideration
Maintenance cost is a factor that can not be ignored when users choose equipment. Disc Granulator structure is relatively simple, fewer parts, daily maintenance is relatively easy, maintenance costs are low. The Rotary Drum Granulator is relatively difficult to maintain due to its complex internal structure and high-precision processing requirements, and requires more professional technicians to maintain and repair. Therefore, in the course of long-term use, the maintenance cost of the Rotary Drum Granulator may be higher than that of the Disc Granulator.
5.Application scenario analysis
Combined with the above analysis, the Disc Granulator is more suitable for processing medium humidity, easy to form organic materials, such as livestock manure, crop straw, etc., suitable for small and medium-sized production lines. The Rotary Drum Granulator is more suitable for the treatment of high humidity, high viscosity materials, such as kitchen waste, sludge, etc., especially for the occasion with high requirements for particle strength and wear resistance.
Users in the choice of Disc Granulator and Rotary Drum Granulator, should be based on their own production scale, raw material characteristics, product requirements and cost budget and other factors for comprehensive consideration. Through scientific comparative analysis and practical investigation, choose the most suitable for their own production needs of granulation equipment, in order to achieve efficient, stable and low-cost production goals. At the same time, with the continuous progress of technology and the continuous development of the market, New Type Organic Fertilizer Granulators such as New Type Organic Fertilizer Two-In-One Granulators, Hydraulic Roller Granulators, etc., will continue to emerge, providing users with more diversified choices.
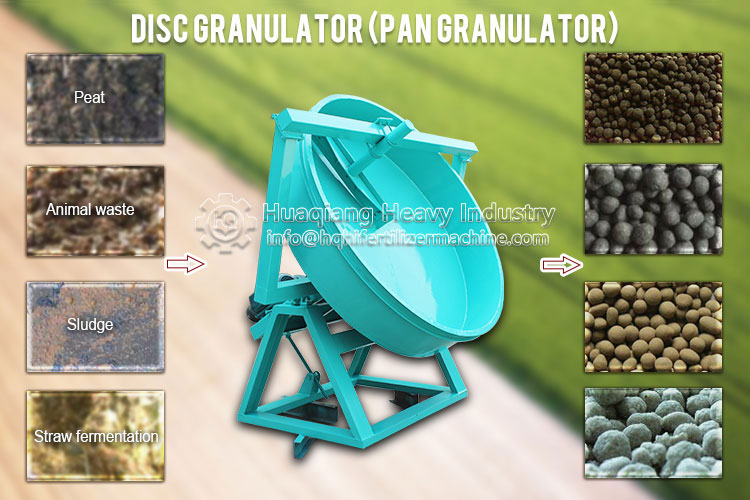
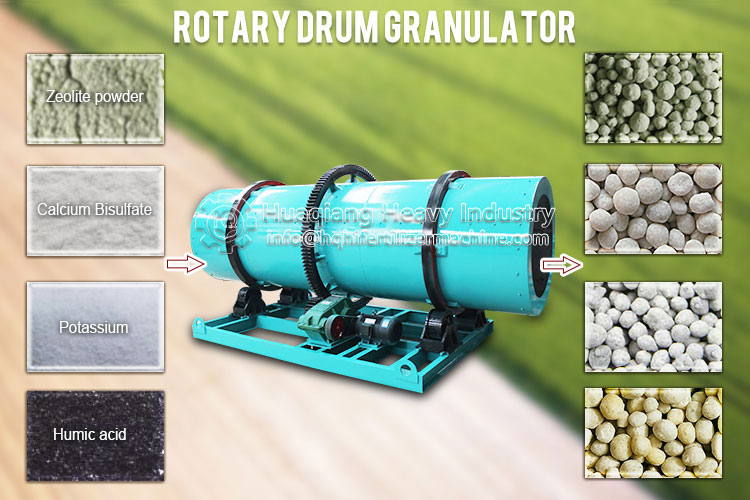
1.Comparison of processing capacity
Disc Granulator with its large working area and moderate speed, good at handling medium humidity, easy to form organic materials. Its continuous operation ability is strong, especially suitable for stable production on large-scale production lines. In contrast, the Rotary Drum Granulator, through its unique rotating structure and internal mixing device, can more effectively deal with high humidity and high viscosity materials to achieve efficient mixing and molding. When dealing with difficult materials, the Rotary Drum Granulator shows greater adaptability and processing capacity.
2. energy efficiency analysis
From the point of view of energy consumption, the Disc Granulator usually has a lower level of energy consumption due to its simple mechanical structure and low operating resistance. However, when handling high moisture materials, additional drying equipment (Drum Fertilizer Dryer) may be required, thus increasing the overall energy consumption. Through its optimized internal structure and efficient mixing mechanism, the Rotary Drum Granulator can reduce energy consumption to a certain extent, especially when dealing with high wet materials, its energy consumption efficiency is relatively higher. However, it is worth noting that the initial investment cost of the Rotary Drum Granulator may be relatively high.
3. Granulation effect evaluation
The granulation effect is one of the important indexes to measure the performance of granulation equipment. The Disc Granulator through its disc surface rolling and friction, so that the material gradually gathered into a ball, the granulation process is relatively mild, the particle shape is more regular, the surface is smooth. The Rotary Drum Granulator through its internal mixing and rolling action, so that the material in the rotation process by strong shear and extrusion, the formation of more compact, uniform particles. In the pursuit of high particle strength and wear resistance, the Rotary Drum Granulator is more advantageous.
4. Maintenance cost consideration
Maintenance cost is a factor that can not be ignored when users choose equipment. Disc Granulator structure is relatively simple, fewer parts, daily maintenance is relatively easy, maintenance costs are low. The Rotary Drum Granulator is relatively difficult to maintain due to its complex internal structure and high-precision processing requirements, and requires more professional technicians to maintain and repair. Therefore, in the course of long-term use, the maintenance cost of the Rotary Drum Granulator may be higher than that of the Disc Granulator.
5.Application scenario analysis
Combined with the above analysis, the Disc Granulator is more suitable for processing medium humidity, easy to form organic materials, such as livestock manure, crop straw, etc., suitable for small and medium-sized production lines. The Rotary Drum Granulator is more suitable for the treatment of high humidity, high viscosity materials, such as kitchen waste, sludge, etc., especially for the occasion with high requirements for particle strength and wear resistance.
Users in the choice of Disc Granulator and Rotary Drum Granulator, should be based on their own production scale, raw material characteristics, product requirements and cost budget and other factors for comprehensive consideration. Through scientific comparative analysis and practical investigation, choose the most suitable for their own production needs of granulation equipment, in order to achieve efficient, stable and low-cost production goals. At the same time, with the continuous progress of technology and the continuous development of the market, New Type Organic Fertilizer Granulators such as New Type Organic Fertilizer Two-In-One Granulators, Hydraulic Roller Granulators, etc., will continue to emerge, providing users with more diversified choices.