Oil palm compost fermentation process
Date:2024/07/29
Key equipment of oil palm compost fermentation process and its application
With the increasing attention to sustainable agriculture and circular economy in the world, the resource utilization of oil palm waste has become a research hotspot. Oil palm compost fermentation is an effective way to convert oil palm waste into organic fertilizer. The key equipment in the process plays a vital role.
In the oil palm compost fermentation process, the equipment configuration in the raw material preparation stage has a direct impact on the subsequent fermentation effect.
The use of a blender is key in the soaking and microbial inoculation stages. Through continuous stirring, the mixer ensures that the microbial microbial agent is evenly mixed with the material, providing good conditions for the growth of microorganisms. In addition, the mixer (Horizontal Ribbon Mixer) can also control the uniformity and depth of microbial inoculation by adjusting the speed and mixing time, thus affecting the subsequent fermentation effect. In actual operation, the parameters of the mixer can be flexibly adjusted according to the characteristics of raw materials and the needs of microorganisms to achieve the best inoculation effect.
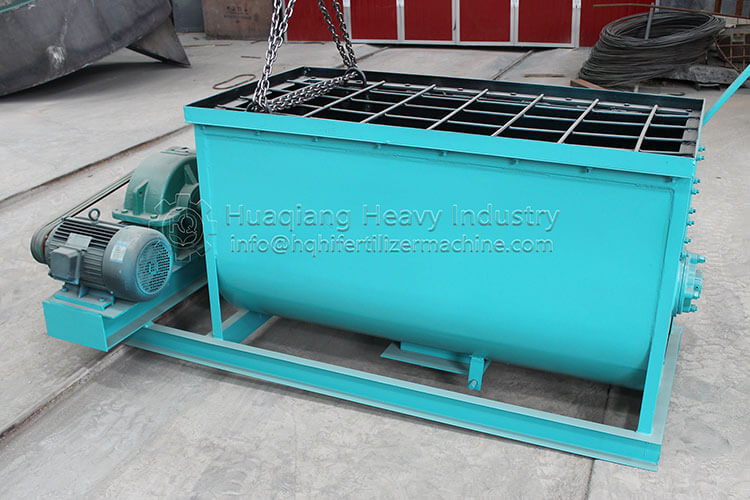
In the compost fermentation stage, the pile turning machine is an essential equipment. Whether they are Windrow Compost Turning Machine、Wheel Type Windrow Compost Turning Machine or Large Wheel Compost Turning Machine, they can turn the pile regularly and promote the aerobic fermentation of the compost. Through the mechanical action of the pile turning machine, the decomposition rate of compost can be accelerated and the maturity of compost can be improved. In addition, the tipping machine can also turn the material in the compost that is not completely decomposed onto the surface of the pile, exposing it to the air and further promoting its decomposition. In actual operation, the frequency and intensity of the turnover machine can be flexibly adjusted according to the fermentation state of the compost and the growth of microorganisms to achieve the best fermentation effect.

Special fermentation equipment plays a key role in the primary and secondary fermentation stages. These devices can precisely control the temperature, humidity and ventilation conditions of the fermentation environment, providing the most suitable environment for the growth of microorganisms. By adjusting the operating parameters of the equipment, such as temperature, humidity and ventilation rate, the metabolic activities of microorganisms can be controlled and the decomposition rate of compost can be accelerated. In addition, the fermentation equipment can also be equipped with sensors and automatic control systems to monitor the indicators in the fermentation process in real time, providing accurate data support for the operator.
In the post-processing stage, the application of equipment such as screening machines, organic fertilizer granulators, dryers, coolers, etc., ensures the quality and consistency of the final product. The screening machine (Rotary Screening Machine)can screen the fermented compost to remove impurities and materials that are not fully decomposed. The organic fertilizer granulator makes the compost material after screening into a granular form, which is convenient for subsequent packaging and transportation. Dryers and coolers are used to reduce the moisture content and temperature of the compost, respectively, to improve its stability and storability. The application of these devices not only improves the added value of products, but also optimizes the production process and reduces the production cost.
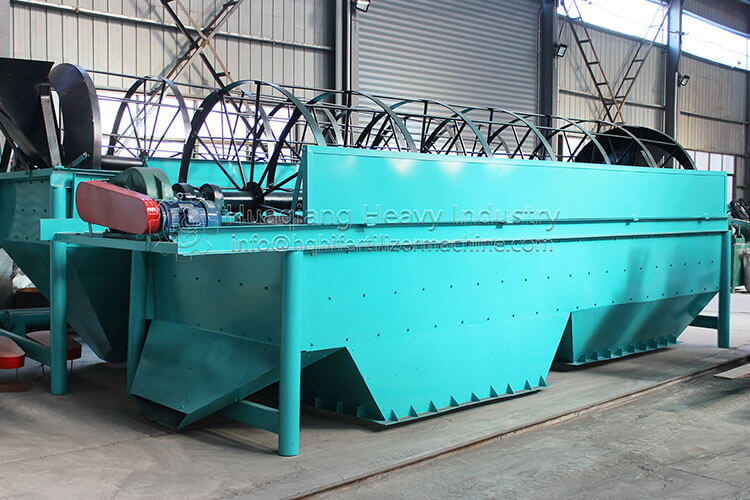
In the entire production process, the application of dust removal and desulfurization equipment and electrical control systems is crucial for environmental protection and automated production. Dust removal and desulphurization equipment can effectively reduce pollutant emissions in the production process and reduce the impact on the environment. At the same time, the electrical control system can realize the automatic control and monitoring of the entire production line, improve production efficiency and product quality. By precisely controlling the operating parameters and working status of each equipment, the optimization and stability of the production process can be achieved to ensure the quality and consistency of the final product.
With the increasing attention to sustainable agriculture and circular economy in the world, the resource utilization of oil palm waste has become a research hotspot. Oil palm compost fermentation is an effective way to convert oil palm waste into organic fertilizer. The key equipment in the process plays a vital role.
In the oil palm compost fermentation process, the equipment configuration in the raw material preparation stage has a direct impact on the subsequent fermentation effect.
The use of a blender is key in the soaking and microbial inoculation stages. Through continuous stirring, the mixer ensures that the microbial microbial agent is evenly mixed with the material, providing good conditions for the growth of microorganisms. In addition, the mixer (Horizontal Ribbon Mixer) can also control the uniformity and depth of microbial inoculation by adjusting the speed and mixing time, thus affecting the subsequent fermentation effect. In actual operation, the parameters of the mixer can be flexibly adjusted according to the characteristics of raw materials and the needs of microorganisms to achieve the best inoculation effect.
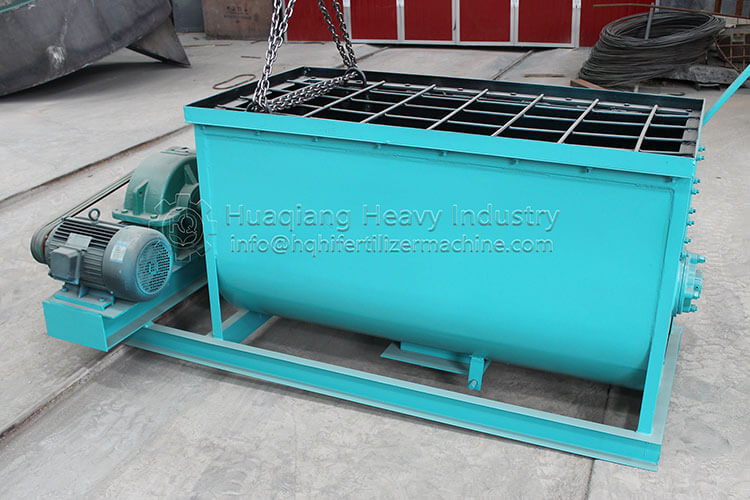
In the compost fermentation stage, the pile turning machine is an essential equipment. Whether they are Windrow Compost Turning Machine、Wheel Type Windrow Compost Turning Machine or Large Wheel Compost Turning Machine, they can turn the pile regularly and promote the aerobic fermentation of the compost. Through the mechanical action of the pile turning machine, the decomposition rate of compost can be accelerated and the maturity of compost can be improved. In addition, the tipping machine can also turn the material in the compost that is not completely decomposed onto the surface of the pile, exposing it to the air and further promoting its decomposition. In actual operation, the frequency and intensity of the turnover machine can be flexibly adjusted according to the fermentation state of the compost and the growth of microorganisms to achieve the best fermentation effect.

Special fermentation equipment plays a key role in the primary and secondary fermentation stages. These devices can precisely control the temperature, humidity and ventilation conditions of the fermentation environment, providing the most suitable environment for the growth of microorganisms. By adjusting the operating parameters of the equipment, such as temperature, humidity and ventilation rate, the metabolic activities of microorganisms can be controlled and the decomposition rate of compost can be accelerated. In addition, the fermentation equipment can also be equipped with sensors and automatic control systems to monitor the indicators in the fermentation process in real time, providing accurate data support for the operator.
In the post-processing stage, the application of equipment such as screening machines, organic fertilizer granulators, dryers, coolers, etc., ensures the quality and consistency of the final product. The screening machine (Rotary Screening Machine)can screen the fermented compost to remove impurities and materials that are not fully decomposed. The organic fertilizer granulator makes the compost material after screening into a granular form, which is convenient for subsequent packaging and transportation. Dryers and coolers are used to reduce the moisture content and temperature of the compost, respectively, to improve its stability and storability. The application of these devices not only improves the added value of products, but also optimizes the production process and reduces the production cost.
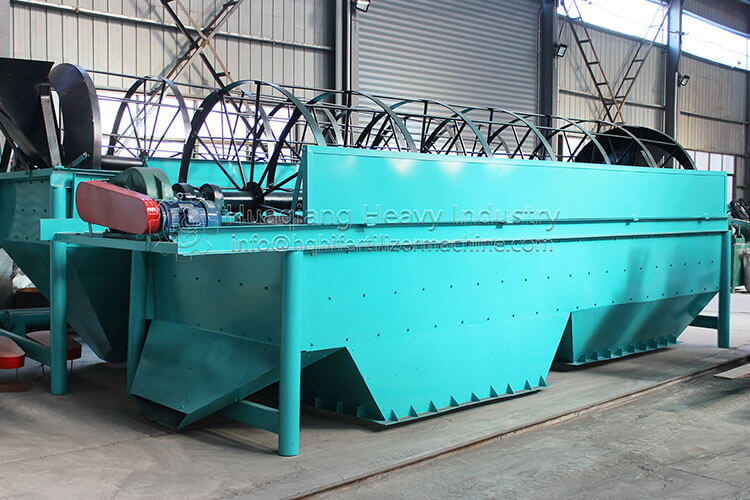
In the entire production process, the application of dust removal and desulfurization equipment and electrical control systems is crucial for environmental protection and automated production. Dust removal and desulphurization equipment can effectively reduce pollutant emissions in the production process and reduce the impact on the environment. At the same time, the electrical control system can realize the automatic control and monitoring of the entire production line, improve production efficiency and product quality. By precisely controlling the operating parameters and working status of each equipment, the optimization and stability of the production process can be achieved to ensure the quality and consistency of the final product.