Go through the second organic fertilizer
Date:2024/08/08
On the road of sustainable agricultural development, the importance of organic fertilizer has become increasingly prominent, which can not only improve soil structure, improve crop quality, but also promote the development of agricultural circular economy. In this green revolution, the wheeled strip composting machine, with its efficient and convenient characteristics, has become a key equipment for processing organic waste such as cow manure and quickly transforming it into high-quality organic fertilizer. Today, let's explore the work flow of this crazy and ingenious machine - wheeled strip compost tiller, and briefly introduce the pelletizer granulation process with it, as well as the process flow of the entire fertilizer production line.
Work flow of wheeled strip compost tiller
Raw material preparation: First of all, the collected organic waste such as cow manure is initially treated, such as removing large impurities and adjusting the moisture content to the appropriate range (generally 50%-60%) to ensure the smooth progress of the subsequent fermentation process.
Pile fermentation: the pre-treated organic materials are stacked in the designated area according to a certain proportion and levels to form a strip shape. This process takes into account the needs of the material for air permeability, water retention and microbial activity.
Heap turning operation: At this time, the wheeled strip compost heap turning machine appears. It uses advanced wheel design, can easily shuttle between the strip, through its powerful flipping ability, the material evenly flip, to achieve the inner and outer layer material exchange, increase the oxygen contact area, promote the reproduction and activity of aerobic microorganisms, accelerate the decomposition and decomposition of organic matter process. Once passed by, the original dull pile suddenly revitalized, the temperature rose, the smell reduced, and the fertilizer effect gradually appeared.
Regular monitoring: During the stacking process, the staff needs to regularly monitor the key parameters of the compost such as temperature, humidity, pH value, and timely adjust the stacking frequency and water supplement to ensure the stable fermentation process.
Mature and stable: After a period of continuous stacking and fermentation, organic matter is gradually transformed into a stable, harmless, and nutrient-rich organic fertilizer. At this time, the fertilizer color becomes dark, the texture is loose, there is no odor, and it meets the standard of use.
Fertilizer production line process flow
1. Raw material collection and treatment
Collection: Organic waste such as cow manure, pig manure, chicken manure, and agricultural waste such as crop straw and rice husk are collected from farms and farmland.
Pretreatment: The collected raw materials are broken, decontaminized, and the water content is adjusted to ensure the uniformity and suitability of the raw materials and lay a good foundation for the subsequent fermentation process.
2. Windrow Compost Turning Machine
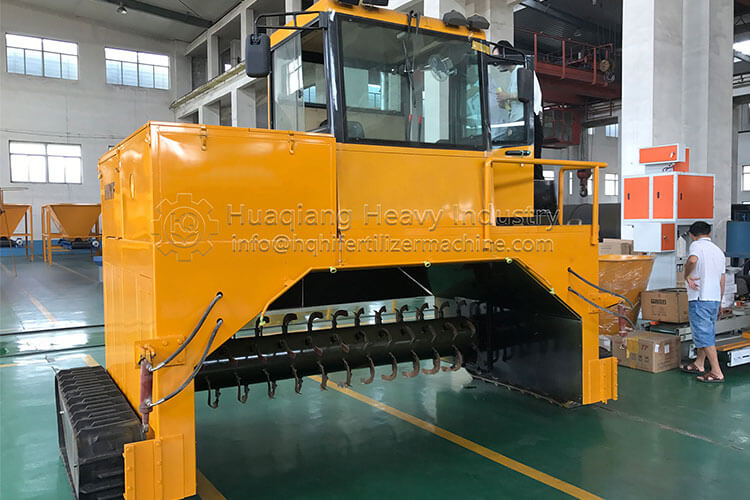
Pile building: The pre-treated raw materials are stacked in the designated area according to a certain proportion and levels, forming a strip shape, easy to manage and turn the pile.
Fermentation: Under aerobic conditions, through the action of microorganisms, the organic matter in the raw material is gradually decomposed, generating heat and carbon dioxide, while forming beneficial substances such as humus. This process requires control of temperature, humidity and oxygen supply to facilitate the smooth fermentation process.
3. Wheel Type Windrow Compost Turning Machine
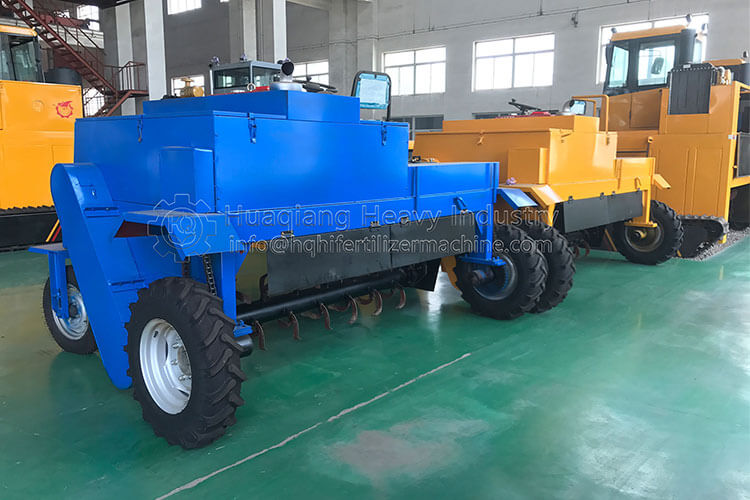
Heap turning operation: The Wheel Type Windrow Compost Turning Machine is used to regularly turn the heap during fermentation, increase the oxygen contact area, promote microbial activity and accelerate the decomposition of organic matter. The reactor temperature and humidity can also be adjusted during the reactor turning process to prevent local overheating or excessive humidity resulting in poor fermentation.
4. Pulverize and sift
Crushing: The compost that is fermented and mature is crushed to break the bulk material and improve the efficiency and product quality of the subsequent process.
Screening: The screening equipment removes impurities and materials that are not fully decomposed to ensure the quality of raw materials entering the next process.
5. Mix ingredients
Ingredients: According to the product formula requirements, different types of raw materials are mixed in a certain proportion to meet the nutrient needs of different crops.
Mixing: The mixing machine is used to fully mix the raw materials after dosing to ensure the balanced distribution of product nutrients.
6. Granulation molding
Rotary Drum Granulator:
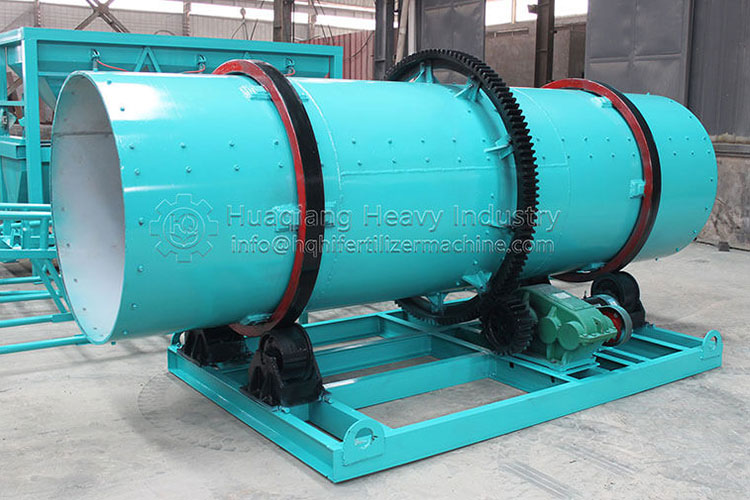
Principle: The Rotary Drum Granulator rolls, extrudates and cuts the evenly mixed material in the roller through the granulation knife or granulation plate installed inside the rotating drum to form granular products.
Features: High production efficiency, regular particle shape, suitable for large-scale production.
Disc Granulator:
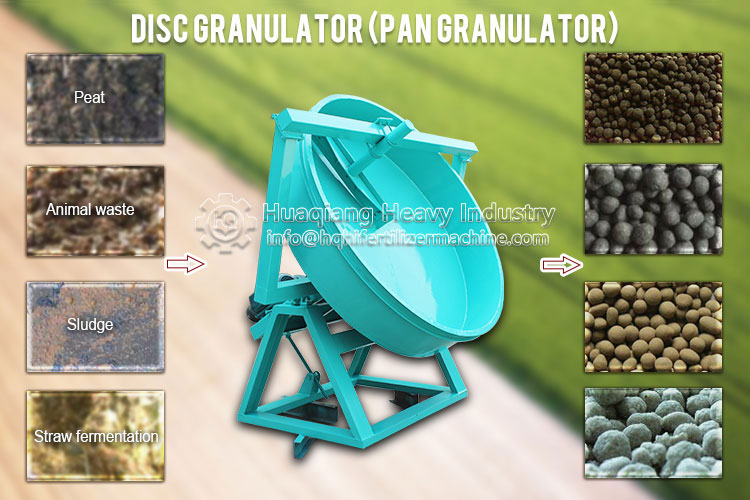
Principle: The Disc Granulator uses a rotating disc to throw the material to the edge and form a material layer, and the material gradually bonds into particles during the rolling and collision process on the edge of the disc.
Features: Simple operation, easy to control particle size and shape, suitable for small batch production and experimental research.
7. Dry and cool
Drying: The fertilizer after granulation is sent into the drying equipment, and the excess water in the particles is removed by hot air or natural wind to improve the stability and storage of the product.
Cooling: After drying, the fertilizer has a high temperature and needs to be cooled to prevent clumping and deterioration, while facilitating subsequent packaging and transportation.
8. Screening and grading
The fertilizer particles after drying and cooling are graded by the screening equipment, and the unqualified large particles and small particles are removed to ensure the uniformity of product quality.
9. Packing and warehousing
The qualified fertilizer particles after screening and grading are measured, packaged, and labeled with product name, nutrient content, production date and other information.
The packaged fertilizer products are stored in the warehouse, awaiting sale or transportation to the field for use.
Through this complete fertilizer production line process, it not only realizes the resource utilization of agricultural waste, but also provides the society with a large number of environmentally friendly and efficient organic fertilizers, which promotes the green transformation and sustainable development of agriculture.
Work flow of wheeled strip compost tiller
Raw material preparation: First of all, the collected organic waste such as cow manure is initially treated, such as removing large impurities and adjusting the moisture content to the appropriate range (generally 50%-60%) to ensure the smooth progress of the subsequent fermentation process.
Pile fermentation: the pre-treated organic materials are stacked in the designated area according to a certain proportion and levels to form a strip shape. This process takes into account the needs of the material for air permeability, water retention and microbial activity.
Heap turning operation: At this time, the wheeled strip compost heap turning machine appears. It uses advanced wheel design, can easily shuttle between the strip, through its powerful flipping ability, the material evenly flip, to achieve the inner and outer layer material exchange, increase the oxygen contact area, promote the reproduction and activity of aerobic microorganisms, accelerate the decomposition and decomposition of organic matter process. Once passed by, the original dull pile suddenly revitalized, the temperature rose, the smell reduced, and the fertilizer effect gradually appeared.
Regular monitoring: During the stacking process, the staff needs to regularly monitor the key parameters of the compost such as temperature, humidity, pH value, and timely adjust the stacking frequency and water supplement to ensure the stable fermentation process.
Mature and stable: After a period of continuous stacking and fermentation, organic matter is gradually transformed into a stable, harmless, and nutrient-rich organic fertilizer. At this time, the fertilizer color becomes dark, the texture is loose, there is no odor, and it meets the standard of use.
Fertilizer production line process flow
1. Raw material collection and treatment
Collection: Organic waste such as cow manure, pig manure, chicken manure, and agricultural waste such as crop straw and rice husk are collected from farms and farmland.
Pretreatment: The collected raw materials are broken, decontaminized, and the water content is adjusted to ensure the uniformity and suitability of the raw materials and lay a good foundation for the subsequent fermentation process.
2. Windrow Compost Turning Machine
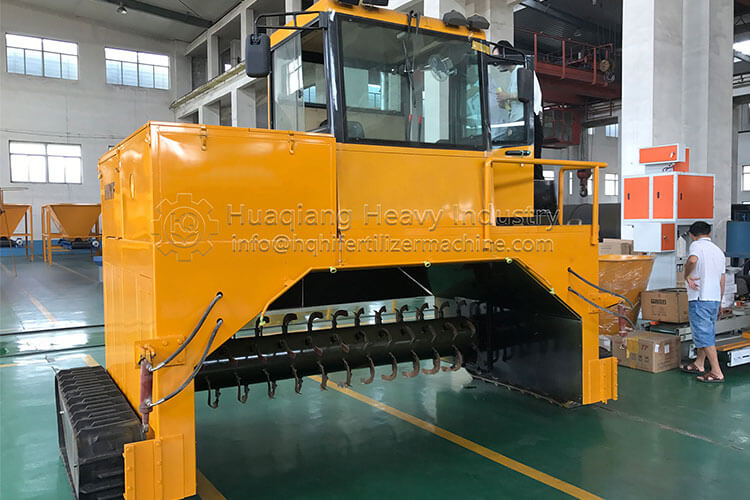
Pile building: The pre-treated raw materials are stacked in the designated area according to a certain proportion and levels, forming a strip shape, easy to manage and turn the pile.
Fermentation: Under aerobic conditions, through the action of microorganisms, the organic matter in the raw material is gradually decomposed, generating heat and carbon dioxide, while forming beneficial substances such as humus. This process requires control of temperature, humidity and oxygen supply to facilitate the smooth fermentation process.
3. Wheel Type Windrow Compost Turning Machine
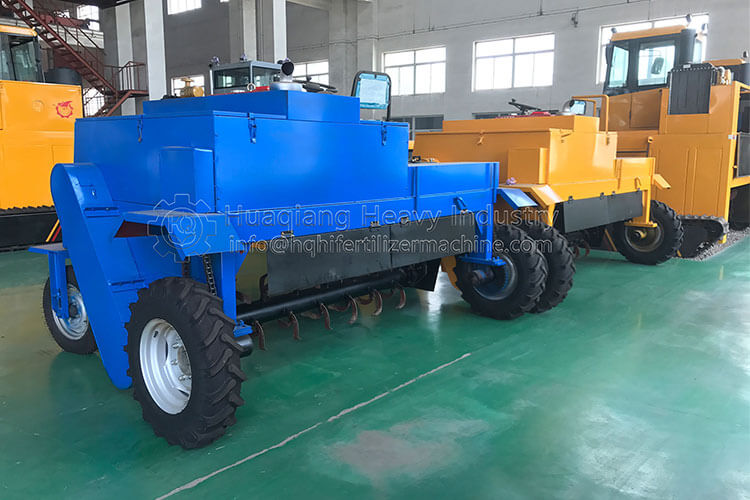
Heap turning operation: The Wheel Type Windrow Compost Turning Machine is used to regularly turn the heap during fermentation, increase the oxygen contact area, promote microbial activity and accelerate the decomposition of organic matter. The reactor temperature and humidity can also be adjusted during the reactor turning process to prevent local overheating or excessive humidity resulting in poor fermentation.
4. Pulverize and sift
Crushing: The compost that is fermented and mature is crushed to break the bulk material and improve the efficiency and product quality of the subsequent process.
Screening: The screening equipment removes impurities and materials that are not fully decomposed to ensure the quality of raw materials entering the next process.
5. Mix ingredients
Ingredients: According to the product formula requirements, different types of raw materials are mixed in a certain proportion to meet the nutrient needs of different crops.
Mixing: The mixing machine is used to fully mix the raw materials after dosing to ensure the balanced distribution of product nutrients.
6. Granulation molding
Rotary Drum Granulator:
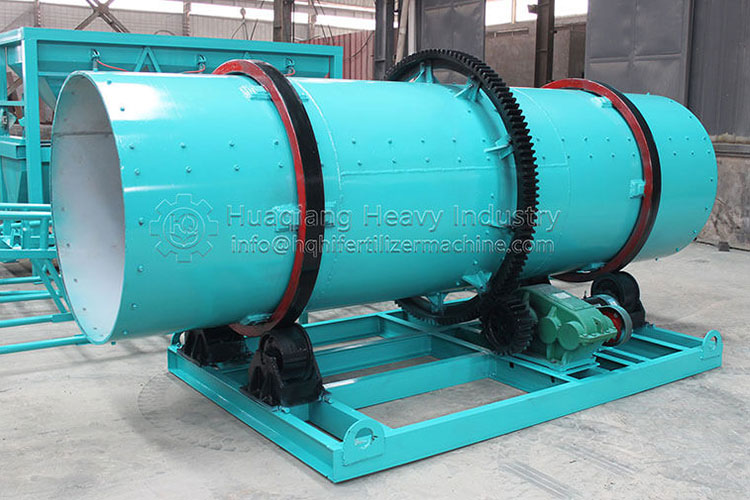
Principle: The Rotary Drum Granulator rolls, extrudates and cuts the evenly mixed material in the roller through the granulation knife or granulation plate installed inside the rotating drum to form granular products.
Features: High production efficiency, regular particle shape, suitable for large-scale production.
Disc Granulator:
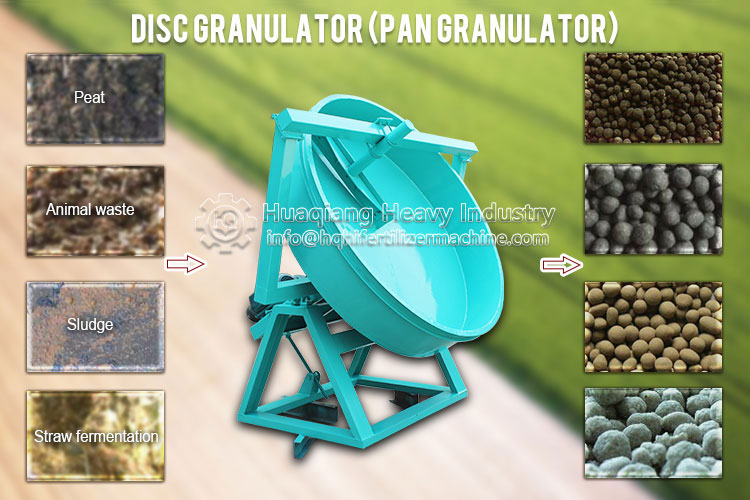
Principle: The Disc Granulator uses a rotating disc to throw the material to the edge and form a material layer, and the material gradually bonds into particles during the rolling and collision process on the edge of the disc.
Features: Simple operation, easy to control particle size and shape, suitable for small batch production and experimental research.
7. Dry and cool
Drying: The fertilizer after granulation is sent into the drying equipment, and the excess water in the particles is removed by hot air or natural wind to improve the stability and storage of the product.
Cooling: After drying, the fertilizer has a high temperature and needs to be cooled to prevent clumping and deterioration, while facilitating subsequent packaging and transportation.
8. Screening and grading
The fertilizer particles after drying and cooling are graded by the screening equipment, and the unqualified large particles and small particles are removed to ensure the uniformity of product quality.
9. Packing and warehousing
The qualified fertilizer particles after screening and grading are measured, packaged, and labeled with product name, nutrient content, production date and other information.
The packaged fertilizer products are stored in the warehouse, awaiting sale or transportation to the field for use.
Through this complete fertilizer production line process, it not only realizes the resource utilization of agricultural waste, but also provides the society with a large number of environmentally friendly and efficient organic fertilizers, which promotes the green transformation and sustainable development of agriculture.