Detailed explanation of organic fertilizer fermentation process and efficiency improvement strategy
Date:2024/07/24
In modern agriculture, the application of organic fertilizers is increasingly widespread, which not only improves soil quality, but also promotes the healthy growth of crops. The fermentation process of organic fertilizer is a crucial part of the entire production process. By introducing and optimizing the use of the above organic fertilizer equipment, not only can significantly improve the fermentation efficiency and product quality of organic fertilizer, but also reduce energy consumption and labor costs, and contribute to the sustainable development of modern agriculture.
Detailed explanation of organic fertilizer fermentation process
The fermentation process of organic fertilizer is mainly divided into several stages: raw material preparation, compost fermentation, maturation stabilization and post-treatment. Raw materials need to be processed by equipment such as Straw Crusher to ensure uniform particle size and facilitate microbial decomposition. Subsequently, the compost fermentation is carried out under the appropriate temperature, humidity and ventilation conditions. At this stage, a Horizontal Mixer can be introduced to turn the pile regularly to ensure sufficient oxygen and accelerate the fermentation process.
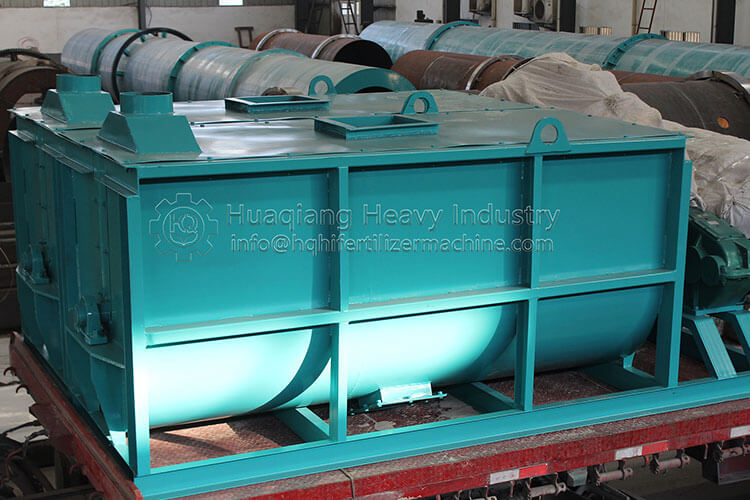
Efficiency improvement strategy
Efficient granulation: The use of New Type Organic Fertilizer Granulator or Hydraulic Roller Granulator, through physical extrusion molding, improve the uniformity of particles and yield, reduce the follow-up screening workload, significantly improve production efficiency.
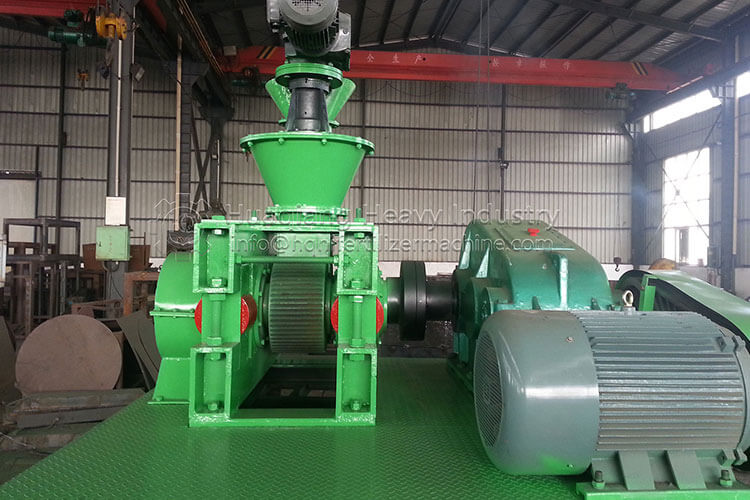
Fine grinding: The use of Chain Crusher and Half-Wet Material Crusher to fine raw materials, to ensure that the size of raw materials meet the requirements of fermentation, accelerate the microbial decomposition speed, shorten the fermentation cycle.
Intelligent mixing: The introduction of automatic control of the Double Axis Mixer or BB Fertilizer Mixer, to achieve accurate ratio and uniform mixing, reduce manual intervention, improve mixing efficiency and quality.
Optimization of drying and cooling: The Drum Fertilizer Dryer is combined with the Drum Fertilizer Cooler unit, which uses the heat exchange principle to quickly remove water, while controlling the temperature, protecting the activity of beneficial microorganisms, and laying a good foundation for subsequent granulation and packaging.
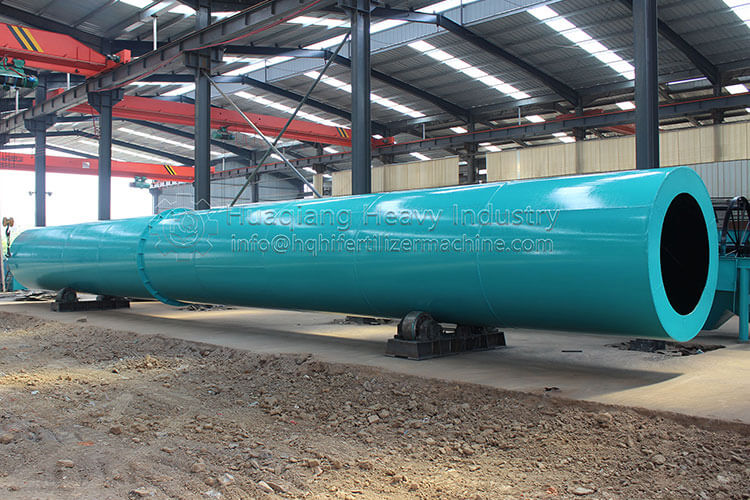
Screening and coating: Accurate screening by Rotary Screener Machine and Vibration Screener Machine ensures consistent product size. Subsequently, the Coating Machine is used for coating treatment to enhance the slow-release and anti-caking properties of the fertilizer and enhance the added value of the product.
Detailed explanation of organic fertilizer fermentation process
The fermentation process of organic fertilizer is mainly divided into several stages: raw material preparation, compost fermentation, maturation stabilization and post-treatment. Raw materials need to be processed by equipment such as Straw Crusher to ensure uniform particle size and facilitate microbial decomposition. Subsequently, the compost fermentation is carried out under the appropriate temperature, humidity and ventilation conditions. At this stage, a Horizontal Mixer can be introduced to turn the pile regularly to ensure sufficient oxygen and accelerate the fermentation process.
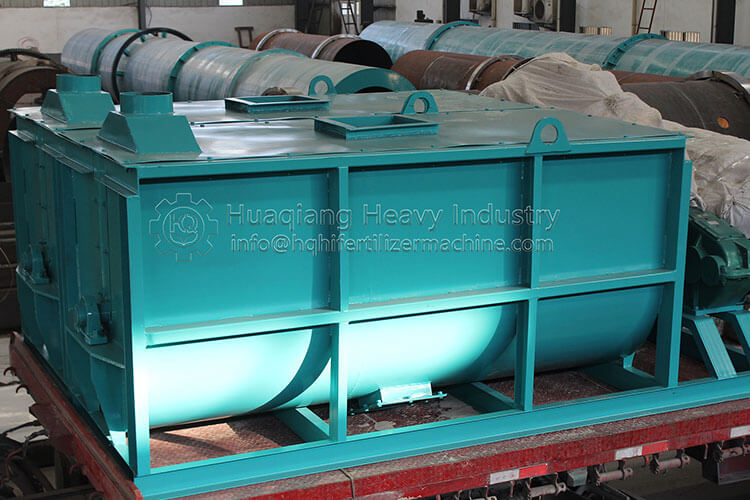
Efficiency improvement strategy
Efficient granulation: The use of New Type Organic Fertilizer Granulator or Hydraulic Roller Granulator, through physical extrusion molding, improve the uniformity of particles and yield, reduce the follow-up screening workload, significantly improve production efficiency.
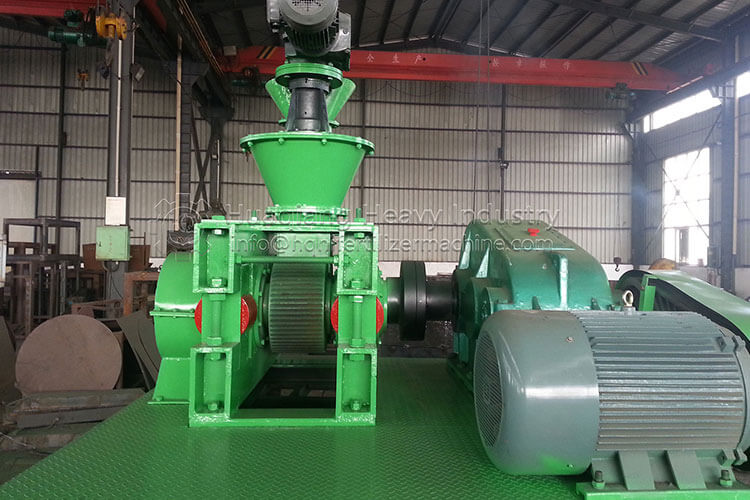
Fine grinding: The use of Chain Crusher and Half-Wet Material Crusher to fine raw materials, to ensure that the size of raw materials meet the requirements of fermentation, accelerate the microbial decomposition speed, shorten the fermentation cycle.
Intelligent mixing: The introduction of automatic control of the Double Axis Mixer or BB Fertilizer Mixer, to achieve accurate ratio and uniform mixing, reduce manual intervention, improve mixing efficiency and quality.
Optimization of drying and cooling: The Drum Fertilizer Dryer is combined with the Drum Fertilizer Cooler unit, which uses the heat exchange principle to quickly remove water, while controlling the temperature, protecting the activity of beneficial microorganisms, and laying a good foundation for subsequent granulation and packaging.
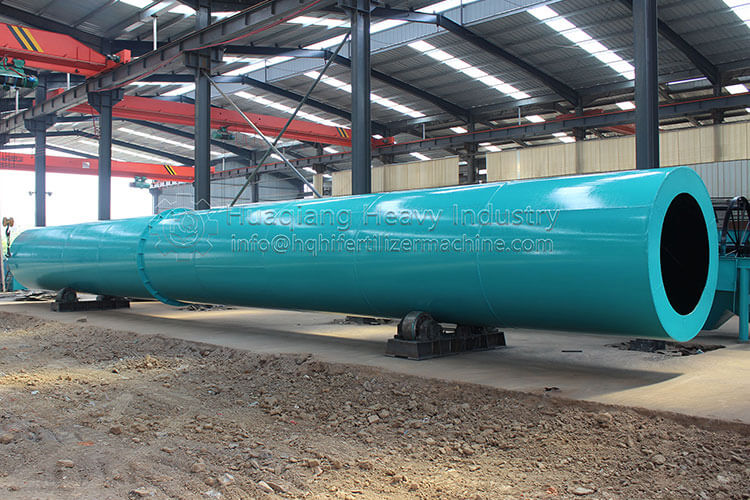
Screening and coating: Accurate screening by Rotary Screener Machine and Vibration Screener Machine ensures consistent product size. Subsequently, the Coating Machine is used for coating treatment to enhance the slow-release and anti-caking properties of the fertilizer and enhance the added value of the product.