What equipment is needed for powdered organic fertilizer production line?
Date:2024/08/07
Small powdered Organic Fertilizer Production Line is mainly used to convert various organic materials, such as chicken manure, pig manure, cow manure, etc., into powdered organic fertilizers rich in nutrients.
Small powdered Organic Fertilizer Production Line usually include the following main parts:
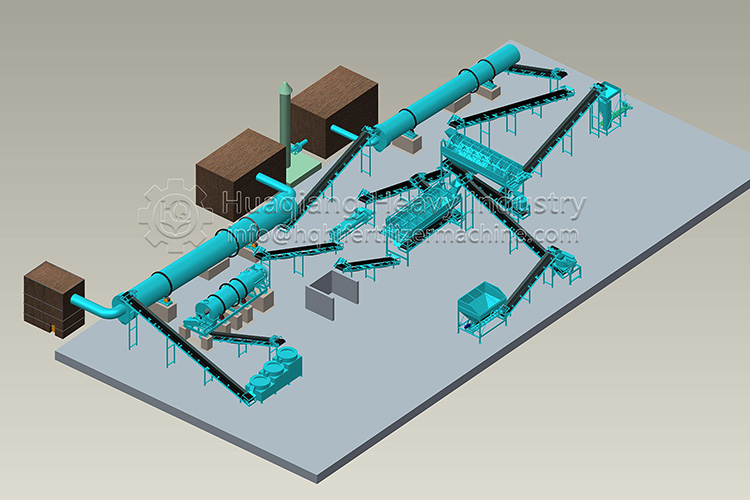
Fermentation system
The fermentation system is the first and most critical step in the entire production line. In addition to traditional natural composting methods, modern small organic fertilizer production lines often employ more scientific and controlled fermentation techniques. The system includes the construction of fermentation tanks or piles, as well as the precise control of temperature, humidity and ventilation conditions. By adding an appropriate amount of microbial agents, the decomposition and decomposition process of organic materials can be accelerated, while reducing the production of harmful substances. The Windrow Compost Turning Machine plays an important role here, which regularly turns the strip to ensure the uniform distribution of oxygen and promote the activity of microorganisms, thereby improving fermentation efficiency and product quality.
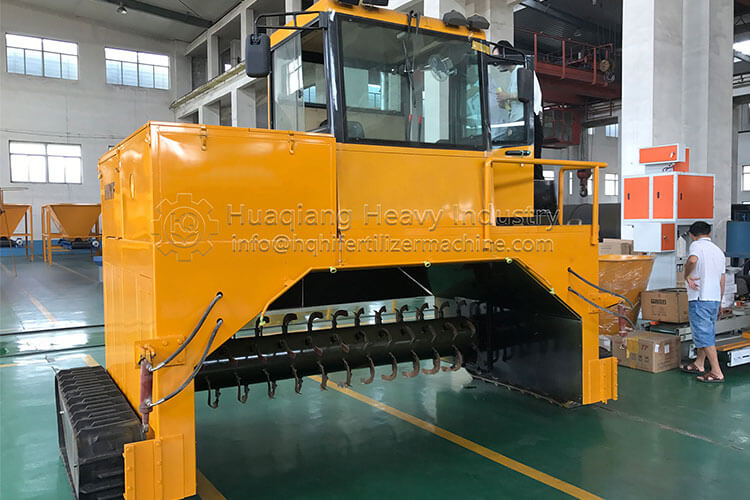
Grinding system
After fermentation, the material enters the crushing system. The crushing equipment used in this process is usually a high-speed rotating blade or hammer, which can effectively break large pieces of material into fine particles. The particle size of the material after grinding is uniform, which is conducive to the subsequent screening and mixing operation. At the same time, the grinding process can further destroy pathogens and parasite eggs in the material, and improve the biosafety of the fertilizer.
Screening system
The screening system classifies the crushed material according to different particle sizes through vibrating screen or roller screen and other equipment. This process removes impurities and non-conforming large or small particles, ensuring the quality of the final product. After screening, the material is more pure, which is conducive to subsequent mixing and packaging.
Agitator mixing system
In the mixing system, different types of organic materials and additives (such as nitrogen, phosphorus, potassium and other nutrients) are mixed according to a preset formula ratio. This process is usually done in a large mixer, which mixes the material thoroughly through rotation or the movement of the mixing arm. The composition of the mixed fertilizer is consistent and can meet the nutritional needs of different crops.
Rotary Drum Granulator
If the production line needs to produce granular organic fertilizer, the Rotary Drum Granulator is the key equipment. After adding the appropriate amount of water and binder into the evenly mixed material, enter the Rotary Drum Granulator. The special structure and rotating motion in the drum make the material gradually form particles during rolling. The granular organic fertilizer produced by the Rotary Drum Granulator is not only beautiful in appearance, but also has good physical properties and is easy to store and transport. In addition, granular fertilizer can reduce dust flying and improve the working environment when applied.
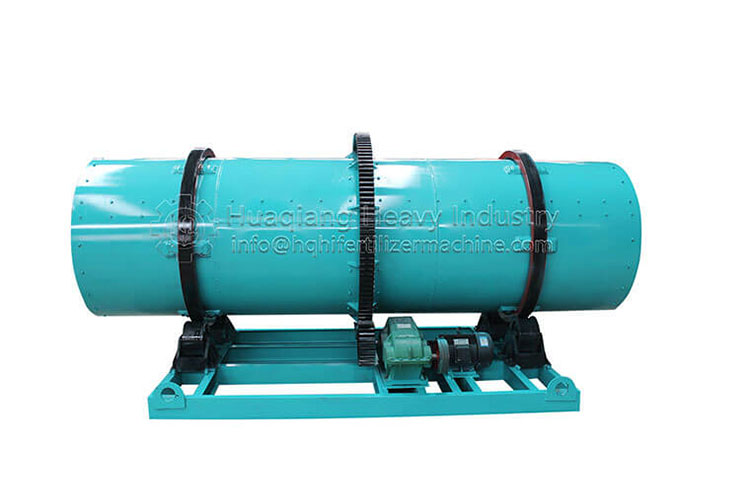
Packaging system
Finally, the mixed or granulated organic fertilizer enters the packaging system. This process includes weighing, sealing and labeling. Modern packaging equipment can automate these operations, improving packaging efficiency and accuracy. Packaged organic fertilizer products are not only convenient for storage and transportation, but also can be displayed to consumers in the market with a more professional image.
Through the introduction of advanced equipment such as roller granulator and strip composting and turning machine, the small powdered organic fertilizer production line realizes the automation and scientific process from raw material fermentation to finished product packaging.
Small powdered Organic Fertilizer Production Line usually include the following main parts:
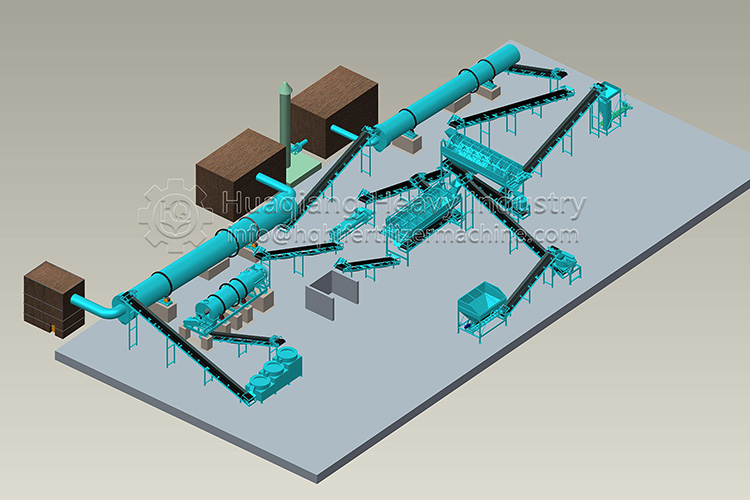
Fermentation system
The fermentation system is the first and most critical step in the entire production line. In addition to traditional natural composting methods, modern small organic fertilizer production lines often employ more scientific and controlled fermentation techniques. The system includes the construction of fermentation tanks or piles, as well as the precise control of temperature, humidity and ventilation conditions. By adding an appropriate amount of microbial agents, the decomposition and decomposition process of organic materials can be accelerated, while reducing the production of harmful substances. The Windrow Compost Turning Machine plays an important role here, which regularly turns the strip to ensure the uniform distribution of oxygen and promote the activity of microorganisms, thereby improving fermentation efficiency and product quality.
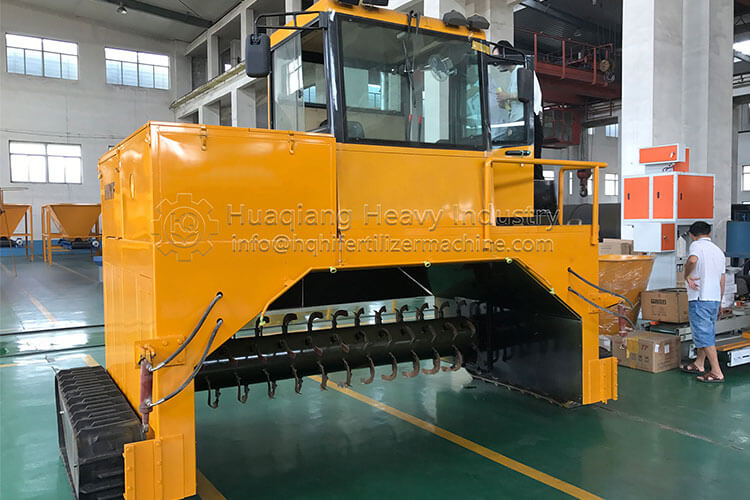
Grinding system
After fermentation, the material enters the crushing system. The crushing equipment used in this process is usually a high-speed rotating blade or hammer, which can effectively break large pieces of material into fine particles. The particle size of the material after grinding is uniform, which is conducive to the subsequent screening and mixing operation. At the same time, the grinding process can further destroy pathogens and parasite eggs in the material, and improve the biosafety of the fertilizer.
Screening system
The screening system classifies the crushed material according to different particle sizes through vibrating screen or roller screen and other equipment. This process removes impurities and non-conforming large or small particles, ensuring the quality of the final product. After screening, the material is more pure, which is conducive to subsequent mixing and packaging.
Agitator mixing system
In the mixing system, different types of organic materials and additives (such as nitrogen, phosphorus, potassium and other nutrients) are mixed according to a preset formula ratio. This process is usually done in a large mixer, which mixes the material thoroughly through rotation or the movement of the mixing arm. The composition of the mixed fertilizer is consistent and can meet the nutritional needs of different crops.
Rotary Drum Granulator
If the production line needs to produce granular organic fertilizer, the Rotary Drum Granulator is the key equipment. After adding the appropriate amount of water and binder into the evenly mixed material, enter the Rotary Drum Granulator. The special structure and rotating motion in the drum make the material gradually form particles during rolling. The granular organic fertilizer produced by the Rotary Drum Granulator is not only beautiful in appearance, but also has good physical properties and is easy to store and transport. In addition, granular fertilizer can reduce dust flying and improve the working environment when applied.
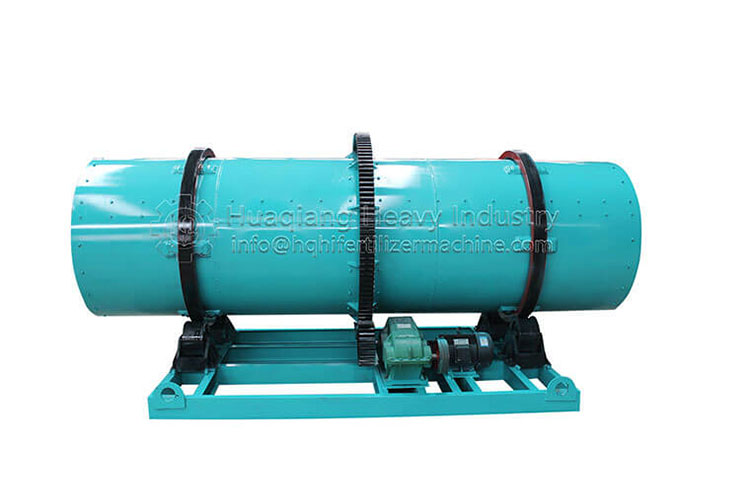
Packaging system
Finally, the mixed or granulated organic fertilizer enters the packaging system. This process includes weighing, sealing and labeling. Modern packaging equipment can automate these operations, improving packaging efficiency and accuracy. Packaged organic fertilizer products are not only convenient for storage and transportation, but also can be displayed to consumers in the market with a more professional image.
Through the introduction of advanced equipment such as roller granulator and strip composting and turning machine, the small powdered organic fertilizer production line realizes the automation and scientific process from raw material fermentation to finished product packaging.